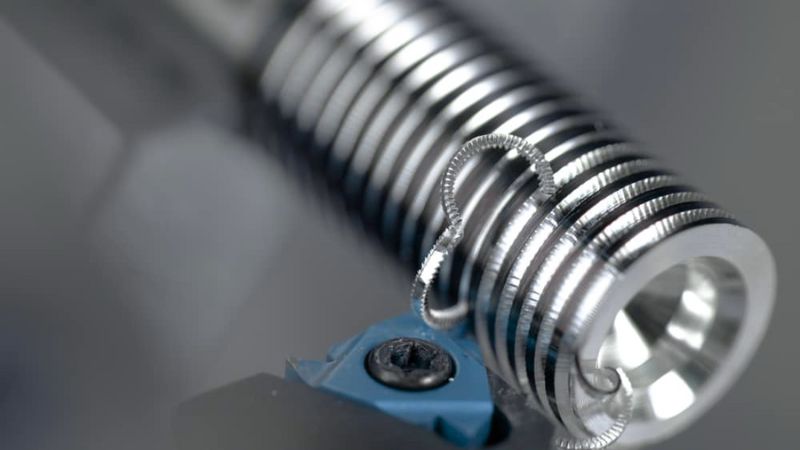
What are Threads?
When you look at a screw, you’ll notice the high points known as the crest and the low points named the root. The flank is the area that connects the crest to the root on each side of the thread.
Threads are essential components in bolts and screws. They provide the grip and mechanical advantage needed to hold things together securely.
Internal threads are found in nuts, and external threads are on bolts or screws. Threads interlock to keep parts in tight alignment. A threaded fastener has a major diameter, which is the largest diameter of the thread, and a minor diameter, the smallest.
The spacing between threads is called the thread pitch, which is crucial for the compatibility between bolts and nuts. Ensuring the thread pitch is uniform is key for maintaining the strength and integrity of the connection.
Types of Threads and Their Uses
The Unified Screw Thread System (USTS) is a standard that classifies threads by series designations: UNC (Unified Coarse), UNF (Unified Fine), and UNEF (Unified Extra Fine).
Coarse threads (UNC) are the most common and offer a good balance between strength and ease of handling.
Fine threads (UNF) provide higher strength and are used when more precise adjustments are needed.
Extra fine threads (UNEF) are less common but allow for even finer adjustments.
Thread Machining Equipment and Tooling
CNC machining centers, particularly lathe machines, are vital for ensuring precision and control during the threading process. For external threads, you will typically utilize a tap and a round die; for internal threads, a tap must be selected based on the specific dimensions of the threaded hole, such as diameter and pitch.
When threading by hand, die stocks are crucial as they provide the necessary grip and alignment for threading dies, ensuring a straight and consistent thread. If your project involves power tools, consider using rigid tapping, a technique that synchronizes the rotation of the tool with the movement of the workpiece, eliminating the need for lead screws and enhancing efficiency.
Additionally, don’t overlook the importance of using cutting fluid or spray to minimize heat generation and extend the lifespan of your cutting tools.
Thread Type | Recommended Tool | Notes |
---|---|---|
External Threads | Tap and Round Die | Ensure proper size and pitch match |
Internal Threads | Tap (specific to hole dimensions) | Match diameter and pitch accurately |
Hand Threading | Die Stock | Provides grip and alignment |
Power Tool Threading | Rigid Tapping | Enhances efficiency |
When selecting a twist drill for pre-threading holes, ensure that its size matches the internal thread specifications you intend to create, including both diameter and depth.
Advancements in Thread Milling and Cutting Tools
The tooling industry has witnessed remarkable advancements, particularly with the development of thread milling tools engineered for enhanced efficiency and precision. These advanced tools can be employed in CNC lathes and milling machines to produce highly accurate and smooth threads.
Recent innovations in materials, such as high-performance ceramic and carbide, have enabled these cutting tools to operate at higher speeds while maintaining durability. Modern thread milling tools also come in a variety of shapes and sizes tailored to meet the specific requirements of your project, allowing for greater versatility and precision in thread machining.
Machining Threading Methods and Processes
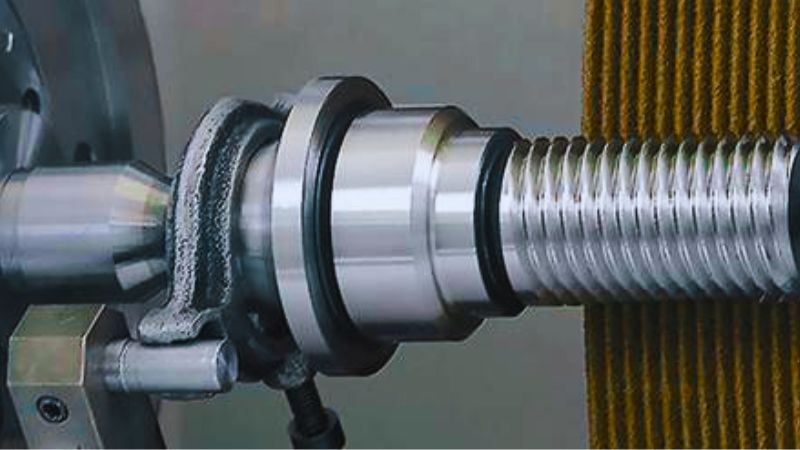
External Thread Cutting Techniques
When you’re cutting external threads, typically on bolts and screws, you use a process that involves removing material to form threads.
One common method is thread cutting using a lathe machine. This involves a single-point cutting tool that follows the helical path of the thread. The tool moves linearly as the workpiece rotates, carving out the thread profile.
Another popular method in CNC machining is thread milling, which can be highly efficient. Here are the basic steps:
- A cutting tool moves circularly around the outer surface of the part.
- As it moves, it cuts deeper into the material, following the helical path of the thread.
Thread milling is versatile since one tool can cut various thread sizes. It’s also faster and provides better thread quality.
Internal Thread Machining: Drilling and Tapping
Moving on to internal threads, which you find in nuts and drilled holes, the first step is usually drilling. This creates a hole for the threads to be machined into. Make sure the hole diameter matches the tap’s requirements for the thread size you’re aiming for.
Post-drilling, you use tapping, which is a process using a tap to cut the thread inside the pre-drilled hole. Here’s how you do it:
- The tap, which looks like a screw, is held in a tap wrench or a CNC machine.
- With consistent pressure, the tap is turned into the hole, cutting threads into the walls of the hole.
Difference Between Thread Rolling and Thread Machining?
Thread rolling is a cold-forming process that involves the deformation of a workpiece to create threads. This method uses cylindrical dies to compress the material, resulting in threads that are stronger and more precise due to the work hardening effect.
The process creates threads without removing material, preserving the integrity of the metal and enhancing its tensile strength.
Futhermore, thread rolling is typically faster than machining, making it suitable for high-volume production. Since there is no cutting involved, the material waste is minimal, which can lead to cost savings.
Thread machining, on the other hand, involves the removal of material to create threads using various cutting tools.
Thread machining can accommodate a wide range of thread types and sizes, making it suitable for custom applications. This method allows for tighter tolerances and finer finishes, which is crucial for components that require exact specifications.
However, thread machining can be applied to a broader variety of materials, including harder metals that may be unsuitable for rolling.
Corprtate with Oukailuo
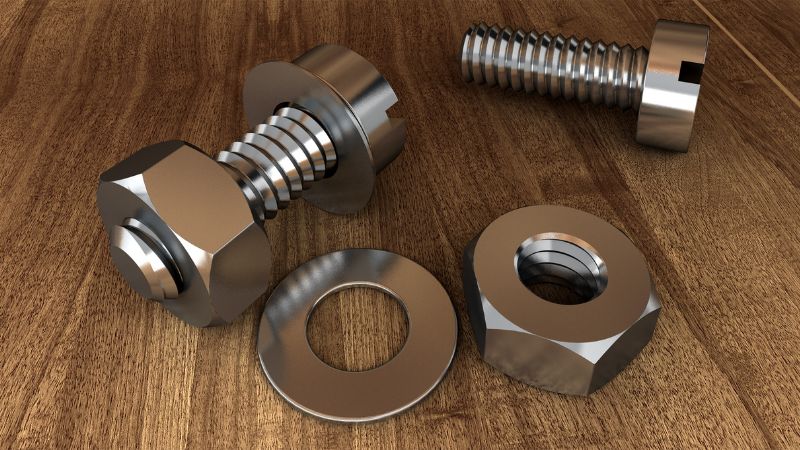
At Oukailuo, we believe in combining cutting-edge technology with exceptional craftsmanship to deliver solutions that perform well.
Explore our range of products on our website and discover how we can help you elevate your project. Thank you for choosing Oukailuo—where quality meets innovation!