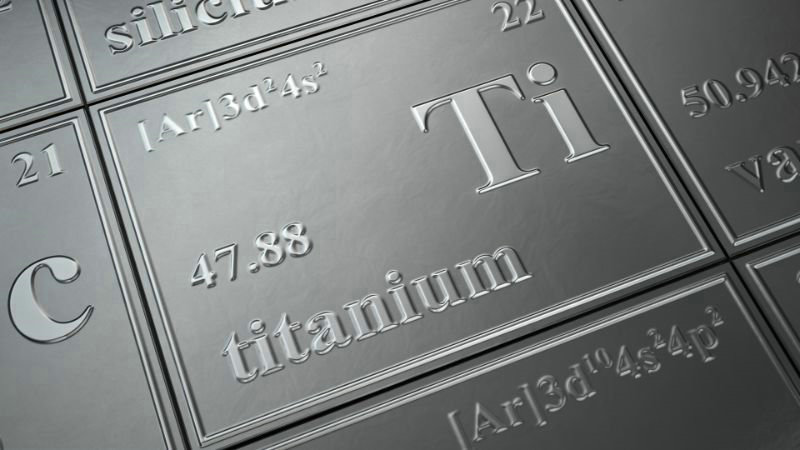
When comparing the strength of titanium and stainless steel, it’s essential to understand their distinct characteristics. Titanium boasts a higher tensile strength than stainless steel, making it the stronger option for many applications. This increased strength, coupled with its lightweight nature, often makes titanium a preferred material in aerospace and other high-performance industries.
Despite stainless steel being a durable and versatile metal, it tends to be heavier and less strong than titanium. Stainless steel is, however, more affordable and widely available in various grades, making it a common choice for everyday use in construction, kitchenware, and medical instruments.
Titanium vs. Stainless Steel: Which Metal is Right for Your Project
Property | Titanium | Stainless Steel |
---|---|---|
Strength | High strength to weight ratio, but lower overall tensile strength compared to stainless steel | Higher overall tensile strength |
Weight | About 50% less dense than stainless steel, making it significantly lighter | Heavier due to higher density |
Corrosion Resistance | Excellent, highly resistant to various corrosive environments including saltwater and some acids | Good, but can corrode in certain environments |
Melting Point | High, around 1668°C, suitable for extreme temperatures | Lower, around 1400-1450°C |
Color | Silver-grey | Can range from silver to gold depending on alloy composition |
Plasticity | Relatively low, making it less malleable | Can be made more malleable by adding alloys |
Machinability | Difficult, requires specialized tools and techniques | Easier, can use standard HSS or carbide tools |
Cost | High, due to rarity and complex processing | Generally more affordable due to readily available raw materials |
Availability | Less readily available, with specific shapes and sizes potentially requiring longer lead times | Widely available in various forms like sheets, tubes, bars, and wires |
Heat Resistance | Good, but performs slightly lower than stainless steel at very high temperatures | Generally performs well at high temperatures |
Biocompatibility | Excellent, making it the preferred material for medical implants | Good, but not as biocompatible as titanium |
Durability | Highly durable and resistant to wear and tear | Durable, but can be less so in certain corrosive environments |
Environmental Impact | Potentially higher upfront environmental cost, but long-term durability can offset this | More sustainable due to recyclability and lower initial environmental impact |
What are Titanium Screws Used For?
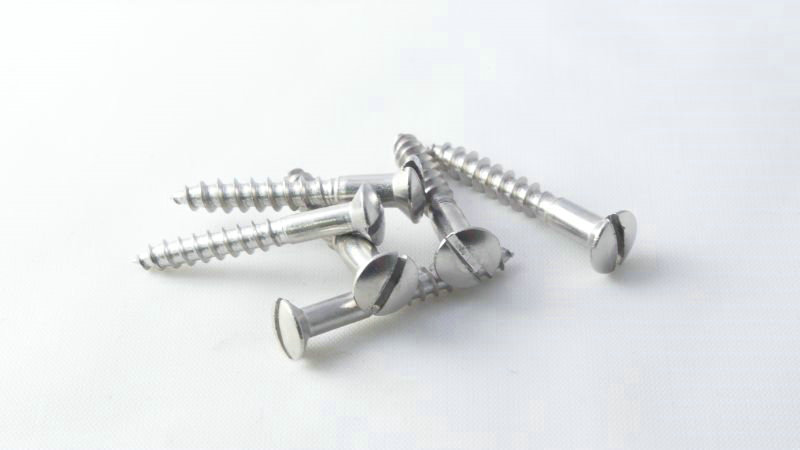
Titanium screws are preferred in high-end applications that require an excellent strength-to-weight ratio, superior corrosion resistance, and biocompatibility. Typical uses include:
- Aerospace: Aircraft components, spacecraft, satellites, etc. to minimize weight while maintaining strength and corrosion resistance.
- Medical implants: Joint replacements, dental implants, spinal fusions, etc. due to titanium’s biocompatibility and non-reactivity with human tissues.
- Marine: Submarine components, deep-sea exploration equipment, and other underwater applications because of titanium’s unparalleled resistance to seawater corrosion.
- Motorsports: High-performance vehicle components like suspension systems, exhaust, etc. to reduce weight while withstanding intense forces.
- Chemical processing: Equipment exposed to harsh chemicals and corrosive environments.
What are Stainless Steel Screws Used For?
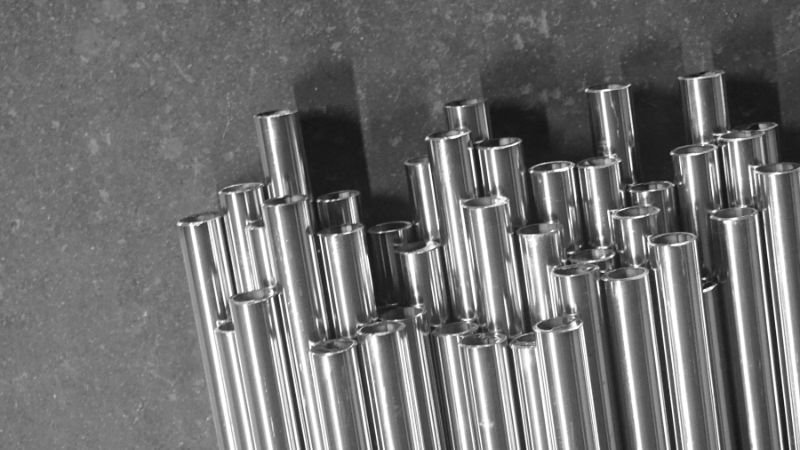
Stainless steel screws are widely used due to their durability, strength, and corrosion resistance. Some common industrial applications include:
- Construction: Securing beams, roofing, siding, and other structural components, especially in outdoor environments.
- Marine and offshore: Boats, docks, piers, and other marine structures due to their resistance to saltwater corrosion, especially 316 grade stainless steel.
- Food processing: Equipment and machinery that come into contact with food, as stainless steel is easy to clean and hygienic.
- Medical equipment: Surgical instruments and medical devices due to stainless steel’s corrosion resistance and ability to be sterilized.
- General fastening: Furniture, cabinetry, decking (305 grade), and many other applications where strength and weather resistance are required.
Frequently Asked Questions
What metal is stronger than titanium?
Materials like certain alloys of steel, such as maraging steel, can surpass titanium in strength. These specialized steels have very high tensile and yield strengths, surpassing the capabilities of titanium alloys in specific scenarios.
Which is better for piercings, titanium or stainless steel?
Titanium is often preferred for piercings due to its biocompatibility and lower risk of causing allergic reactions. Stainless steel can also be safe if it is surgical grade, but it contains nickel, which may cause irritation for some people.
In terms of jewelry, should I choose titanium or stainless steel?
Choose titanium if you want lightweight yet durable jewelry that is resistant to corrosion and hypoallergenic. Stainless steel offers more design flexibility and tends to be more affordable but is heavier and may cause allergies due to its nickel content.
What are the disadvantages of titanium compared to stainless steel?
Titanium is more expensive and harder to machine than stainless steel. Additionally, while it excels in being lightweight and strong, it is not as readily available and can be more challenging to weld compared to stainless steel.