Bolts, often overlooked due to their small size, play a crucial role in multiple industries. As one of the most widely used parts in equipment today, it serves to securely connect different objects, ensuring strength and stability in various applications. However, when bolts become loose, they can lead to a series of issues that can influence the safety and efficiency of the entire system. In this article, we will focus on the reasons why they become loose and how to effectively prevent them to ensure the stable working of your machinery.
What are Loose Bolts?
Bolts are mechanical fasteners designed to join two or more components together by clamping them with a preload. This level of tension(preload) creates friction between the mating surfaces, which prevents separation and distributes loads evenly.
While loose bolts refers to a condition where a bolt has lost its tightness. When this happens, it can pose a significant safety hazard.
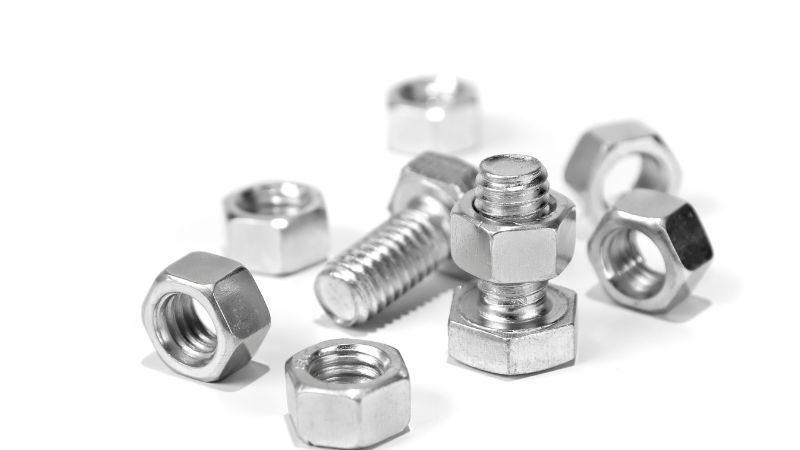
Why is Bolt Loosening So Important?
Bolt loosening issues cannot be ignored. When it happens, it can lead to a number of serious consequences, including reduced structural integrity, abnormal vibration, potential safety hazards, low efficiency and performance, and high repair costs.
In the industrial field, loose bolts can affect the performance of equipment as well as its normal operation. It may also lead to the dislodgement of equipment parts, resulting in production accidents and thus threatening people’s lives.
In the aerospace industry, it may affect the spacecraft’s control system, making it difficult to accurately detect the orbit. This could result in the spacecraft deviating from its intended orbit, increasing the risk of collision with other celestial bodies or space debris.
In transportation, loose bolts on railroad tracks can cause derailments. While in mining equipment, they can lead to the breakdown of machinery and potential injuries to operators.
The series of negative consequences are beyond your imagination. So, it is important to pay attention to the bolt loosening issues to ensure normal operation of various systems and structures. Regular inspections and timely preventive measures can help avoid the risks.
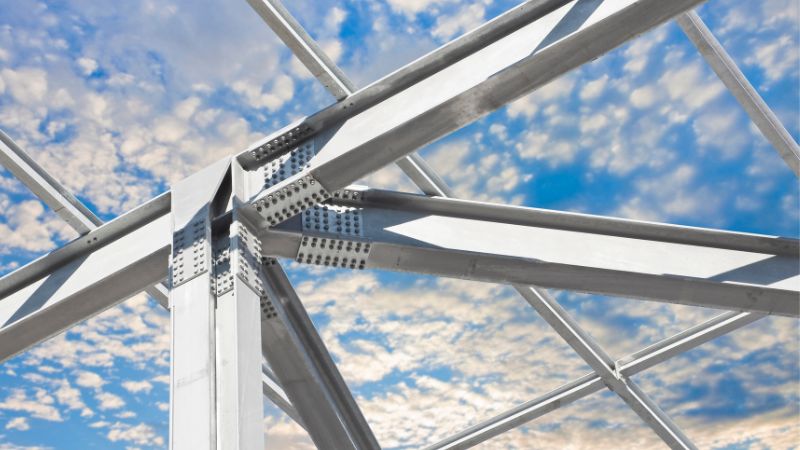
Top 5 Causes of Loose Bolts
- Incorrect Installation
It refers to the failure to apply proper torque when installing the bolts. Over-tightening can cause the bolt to stretch excessively or even break, while under-tightening makes the joint does not have enough clamp force to hold the joint together.
- Material Wear and Tear
Due to the long-time use of the equipment, the bolted joint and fastening materials may undergo deterioration, wear or corrosion, which gradually reduces the friction between the bolt and the material it is securing. Without adequate friction, the bolt is more prone to self-loosening.
- Vibration
Vibration can loosen the bolted joints. When they are exposed to dynamic loads and vibration, the threads of them and nut will work against each other, leading to a reduction in the friction that holds them together. Vibration and shock may also cause the bolt to rotate slightly on its own, which is called spontaneous loosening.
- Manufacturing Defects
Defects in the manufacturing process can affect bolts’ performance. These defects may include improperly machined threads, bad material quality, or inconsistent dimensions. These defects can make it difficult to achieve a secure fit and increase the likelihood of the bolt loosening over time.
- Thermal Expansion
The differential thermal expansion is another factor to consider. Keep the material of the bolt the same as the joint. If the coefficients of these two are inconsistent, changes in temperature can lead to relative movement between them, which may subsequently cause the joint to lose.
5 Signs of Loose Bolts
We have recognized the seriousness and what triggers them, so how can you tell whether your bolts are functioning properly or already showing signs of loosening? Here are 5 signs that help you to indicate:
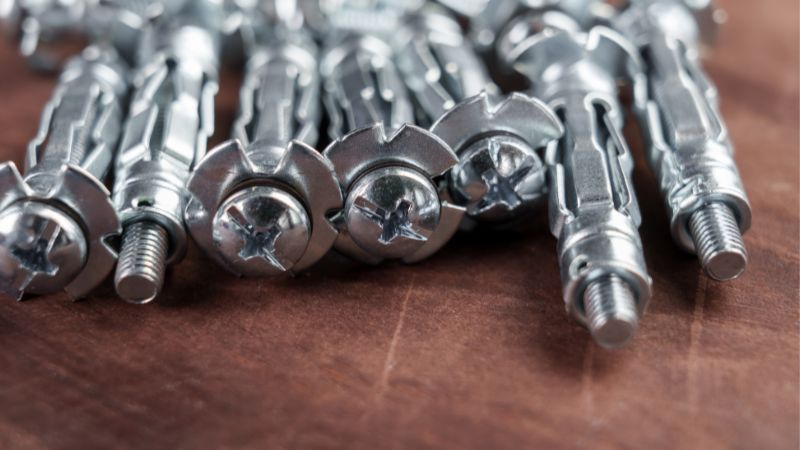
- Gaps:Visual inspection is the most direct way to determine the issue. If there are obvious gaps between the bolt head or nut and the connected parts, or if there are signs of loosening in the tightened portion, these may lead bolted joint to loose.
- Abnormal Sounds: If a bolt begins to loosen, it may produce some noises during the operation of the equipment. These sounds may be continuous or intermittent.
- Decreased Preload: Preload refers to the force applied when a bolt is tightened. If the bolt loosens, its preload will decrease, making the equipment less stable or even worse, fail to work.
- Increased Vibrations: When a bolt loosens, the vibrations of the equipment may increase. This is because bolt loosening can lead to increased gaps between the connected parts, thereby increasing the amplitude of vibrations.
- Stress Relaxation: Under long-term loads, the stress within the bolt material can gradually decrease, resulting in a reduction in bolt pretension. If not solved immediately, it can lead to loosening of the bolts.
Recognizing these signs is crucial, as loosening of bolts can lead to catastrophic tragedy. It’s important to catch any loosening early to prevent potential hazards and damage.
How to Prevent Bolts Becoming Loose?
After analysing the causes and signs of loose bolts, then we will introduce some methods to help prevent this problem. Make sure bolts are installed using the correct tools and techniques. These methods can be divided into friction locking, mechanical locking and permanent locking methods.
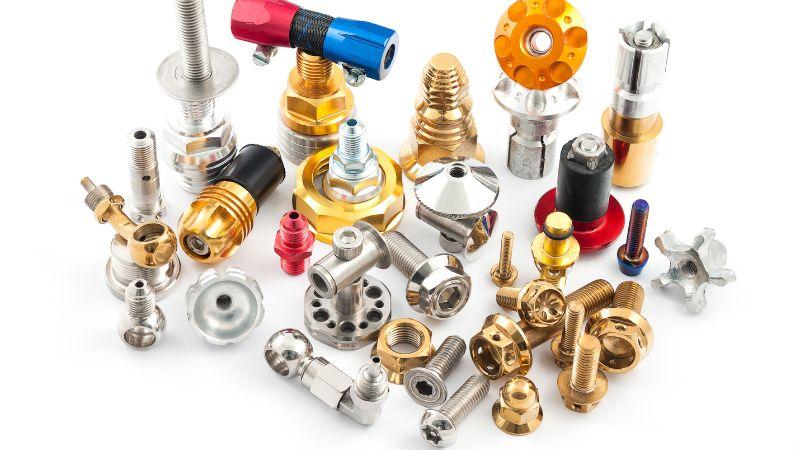
Friction Locking
- Spring Washers: They are designed to produce a spring effect that helps maintain tension on the screw, thereby preventing it from loosening. However, for high-strength bolts and hard materials, they cannot work effectively.
- Self-Locking Nuts: This kind of nuts work by deforming their elastic base when twisted onto a bolt, applying a counter force to prevent vibration.
- Double Nuts: Using two nuts tightened against each other can be able to provide additional friction to prevent loosening.
Friction locking tends to loosen easily when the screw is subject to strong impact, necessitating the use of a marker pen for identification and special attention to ensure no related parts are missing.
Mechanical Locking
- Cotter Pins: These are usually used with slotted nuts. They are combined to lock two parts together by passing through holes in both parts and bending the ends to prevent removal.
- Slotted Nuts: These nuts have a slot that is used to ensure the locking device to be inserted to prevent rotation.
- Lock Washers: These washers have teeth or serrations that bite into the mating surface to prevent separating.
- Locking Wires: Wires are threaded through holes in the bolt heads and nuts to secure them together.
Mechanical locking is relatively reliable and suitable for critical connections, but it also requires that related components remain intact and undamaged.
Permanent Locking
- Welding: By applying electric current to create a weld, this process melts a small area of the bolt and nut, causing them to fuse together and form a solid connection.
- Riveting: A rivet is inserted through a pre-drilled hole in the bolt and nut, and then the end of the rivet is deformed or flattened to secure the bolt and nut together.
- Punching: Dimples on the surface of bolts and nuts created by punching will add friction and resistance, preventing them from turning.
- Bonding: Adhesives can be applied to the surfaces of the bolt and nut. The adhesive creates a strong and cohesive force between the bolt and nut, preventing them from separating.
Permanent locking ensures a tight connection between bolts and nuts, however, it compromises the thread fasteners during disassembly, making them non-reusable.
Each locking method has its own pros and cons. The choice of method depends on the application.
Conclusion
The impact of nuts and bolts coming loose can be significant. By understanding the root causes and applying a proactive approach to it, you can effectively mitigate the risks.