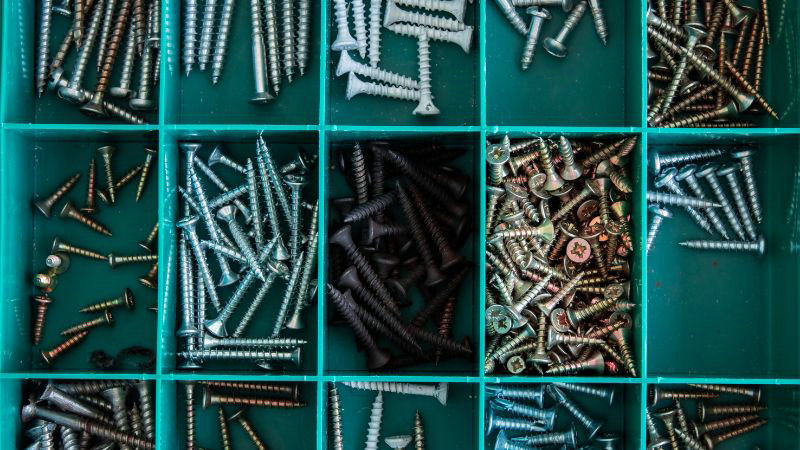
What are Fastener Coatings?
Fastener coatings are crucial for enhancing the durability and functionality of fasteners. They provide protection against corrosion, improve appearance, and can be made from various materials to meet specific needs.
Fastener coatings are layers applied to metal parts, like screws, bolts, and nuts, to protect them from corrosion, which happens when metal starts to wear away due to weather or chemicals.
Why do fasteners need coatings?
Your choice of fastener and coating solution can make a big difference, especially in industries where durability and precision are critical.
For environments like the ocean, where saltwater and moisture are concerns, stainless steel fasteners can help prevent rust.
In the healthcare sector, fasteners are often used in medical devices and equipment. Here, coatings must not only protect against corrosion but also meet stringent cleanliness and non-toxicity standards.
Here are the reasons why fasteners need coating:
- Corrosion Resistant:
- Preventing Rust: Many fasteners are made of steel or other metals susceptible to rust and corrosion when exposed to moisture and environmental elements.
- Enhanced Durability:
- Withstanding Wear and Tear: Coatings can improve the hardness and abrasion resistance of fasteners, making them more durable under mechanical stress.
- Electrical Insulation:
- Preventing Short Circuits: In electrical applications, coated fasteners can act as insulators, preventing unwanted electrical conduction between components.
- Specialized Performance:
- Heat Resistance: In high-temperature environments, certain coatings can protect fasteners from heat-induced degradation.
- Chemical Resistance: In settings where fasteners are exposed to chemicals or harsh substances, specialized coatings ensure that the fasteners maintain their integrity and performance.
Different Types of Fastener Coatings
When choosing fasteners, it’s key to consider the right type of coating that’ll offer the protection and qualities you need. Let’s take a closer look at the various coatings available.
Metallic Coatings
Zinc Plating
Zinc plating is a widely used, cost-effective method to protect fasteners from corrosion. It involves coating the metal surface with a thin layer of zinc, which acts as a sacrificial barrier against rust.
- Clear Zinc
- Appearance: Silver-like finish.
- Advantages: Offers corrosion resistance while maintaining the metallic appearance of the fastener. Suitable for applications where aesthetics are important.
- Applications: Automotive components, electronic housings, and decorative hardware.
- Yellow Zinc
- Appearance: Distinctive golden hue.
- Process: Achieved through an electroplating process that incorporates alloying elements with zinc.
- Advantages: Enhanced resistance to atmospheric corrosion compared to clear zinc. Provides a more aesthetically pleasing finish for certain applications.
- Applications: Architectural fasteners, outdoor structures, and furniture hardware.
Hot Dip Galvanizing
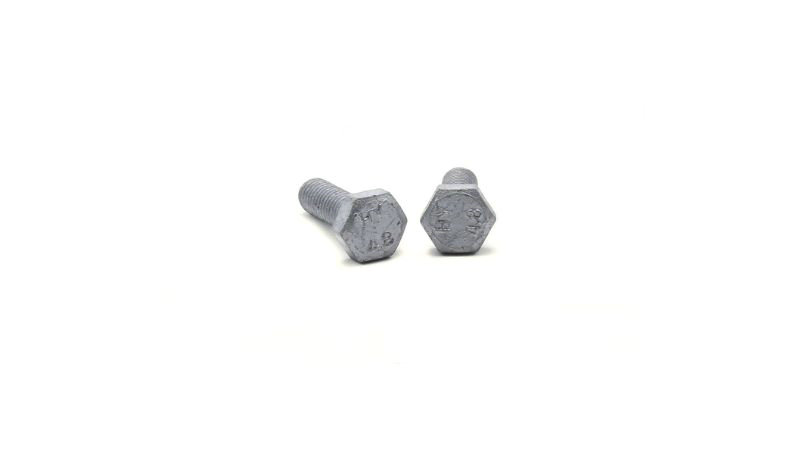
Hot dip galvanizing involves immersing fasteners in molten zinc at high temperatures, resulting in a thick and rugged zinc coating.
- Advantages:
- Durability: Provides superior corrosion protection, especially in harsh outdoor environments.
- Thickness: The coating thickness is significantly greater than that of electroplated zinc, offering prolonged protection.
- Self-Healing: If the coating is scratched, the surrounding zinc can corrode preferentially, protecting the underlying metal.
- Applications: Bridge construction, marine hardware, highway guardrails, and outdoor scaffolding.
Cadmium Plating
Cadmium plating offers excellent corrosion resistance, particularly in high-reliability applications.
- Advantages:
- Corrosion Resistance: Highly effective in preventing corrosion, especially in marine environments.
- Lubricity: Provides a smooth surface that reduces friction and galling between fasteners.
- Solderability: Facilitates easy soldering without damaging the coating.
- Environmental Considerations: Cadmium is toxic and poses environmental and health risks. Its usage is restricted in many industries, leading to a decline in popularity.
- Applications: Aerospace fasteners, military hardware, and specialized electronics.
Nickel Plating
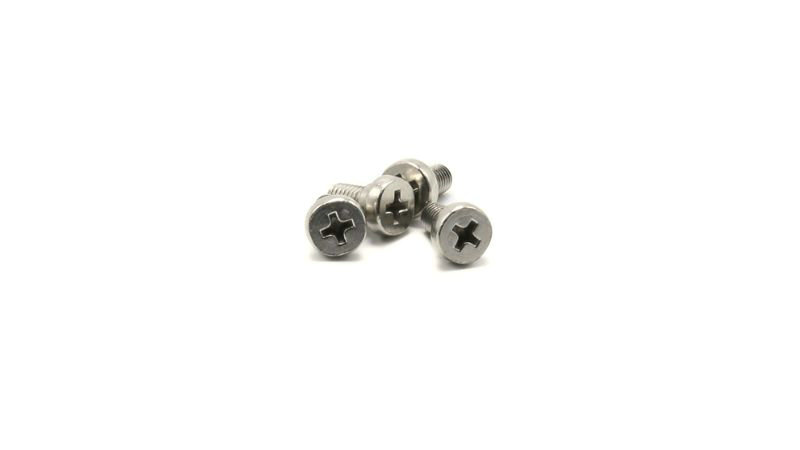
Nickel plating is prized for its hard, lustrous finish and excellent corrosion resistance. It comes in various forms, each tailored for specific applications.
- Watts Nickel Plating
- Characteristics: Provides a bright, uniform coating with good ductility.
- Advantages: Offers excellent corrosion resistance and is suitable for components requiring intricate detailing.
- Applications: Automotive parts, aerospace components, and household hardware.
- Nickel Sulfamate
- Characteristics: It features a smoother and more uniform finish than Watts plating.
- Advantages: Greater conductivity, reduced internal stress, and better dimensional stability. Ideal for subsequent coating processes.
- Applications: Precision machinery parts, electrical components, and decorative hardware.
- Hard Nickel
- Characteristics: Exhibits increased hardness and wear resistance.
- Advantages: Enhances the durability and longevity of fasteners subjected to high-stress conditions.
- Applications: Industrial fasteners, tooling, and high-performance automotive parts.
- Black Nickel
- Characteristics: Provides a sleek, dark finish through specialized plating processes.
- Advantages: Combines aesthetic appeal with corrosion resistance. Often used for decorative purposes where a non-reflective surface is desired.
- Applications: Decorative hardware, architectural fasteners, and consumer electronics.
Chrome Plating
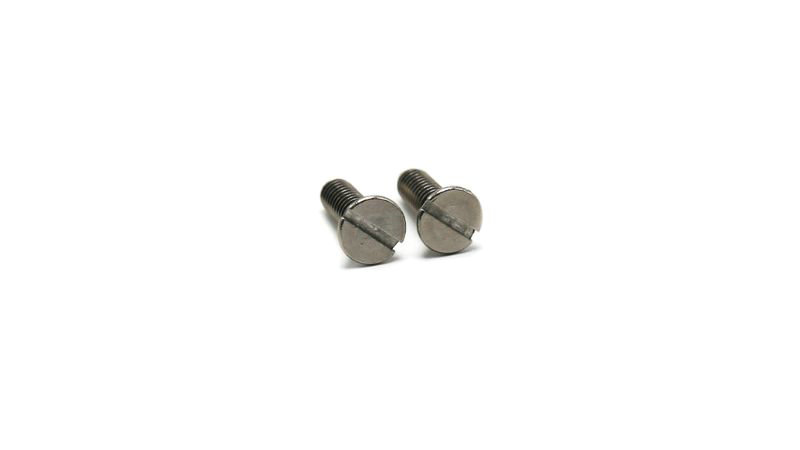
Chrome plating involves applying a layer of chromium onto the fastener’s surface, resulting in a hard, shiny finish.
- Advantages:
- Hardness: Extremely durable and resistant to wear and abrasion.
- Corrosion Resistance: Offers excellent protection against rust and tarnishing.
- Aesthetic Appeal: A highly reflective surface enhances the appearance of fasteners.
- Types:
- Decorative Chrome: Primarily for aesthetic purposes with thinner coatings.
- Hard Chrome: Thicker application for enhanced durability and functionality.
- Applications: Automotive trims, high-end machinery fasteners, and decorative hardware.
Anodizing
While not a traditional coating, anodizing is an electrochemical process that increases the thickness of the natural oxide layer on aluminum fasteners.
- Advantages:
- Corrosion Resistance: Significantly improves the natural resistance of aluminum to corrosion.
- Wear Resistance: Enhances surface hardness, reducing wear from friction.
- Color Stability: Can be dyed in various colors for aesthetic customization.
- Applications: Aerospace fasteners, electronic housings, and architectural hardware.
Non-Metallic Coatings
Phosphate Coatings
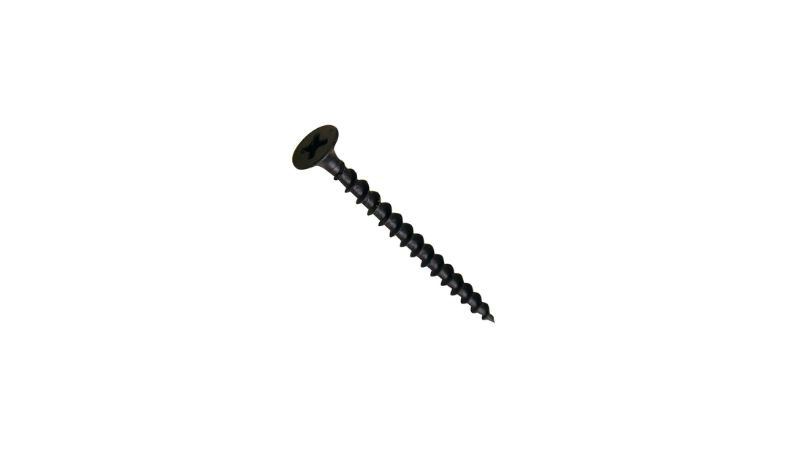
Phosphate coatings are applied to metal surfaces to enhance paint adhesion and reduce surface friction.
- Advantages:
- Corrosion Resistance: Provides a protective barrier against moisture and contaminants.
- Preparation for Coating: Acts as a primer for subsequent paint or powder coatings, ensuring better adhesion and longevity.
- Lubricity: Reduces friction, which minimizes wear during assembly.
- Types:
- Zinc Phosphate: Offers good corrosion resistance and is commonly used for paint priming.
- Manganese Phosphate: Provides excellent wear resistance and is used in applications requiring high durability.
- Applications: Automotive fasteners, machinery parts, and construction hardware.
Black Oxide
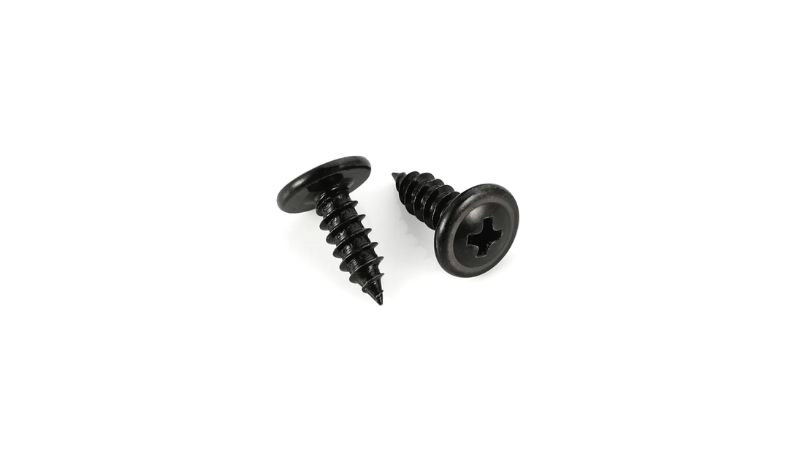
Black oxide is a conversion coating that produces a black finish on ferrous materials through a chemical reaction.
- Advantages:
- Aesthetic Appeal: Provides a sleek, matte black appearance.
- Minimal Corrosion Protection: While it offers some resistance, it’s primarily used for cosmetic purposes.
- Enhanced Lubricity: Improves the fastener’s surface for reduced friction.
- Limitations: Offers limited corrosion protection and is often combined with additional coatings for enhanced durability.
- Applications: Decorative fasteners, firearm components, and electronic device hardware.
Mechanical Plating
Mechanical plating involves embedding metal powders (such as zinc, cadmium, or tin) into the surface of fasteners through a cold welding process.
- Advantages:
- Corrosion Protection: Provides a protective layer without the need for high-temperature processes.
- Uniform Coverage: Ensures even distribution of the coating, including recessed areas.
- Reduced Stress: As it is a cold process, it minimizes thermal stress on the fastener.
- Applications: Fasteners used in electronics, automotive assemblies, and precision machinery.
Organic Coatings
Zinc Flake Coating
Zinc flake coatings combine zinc and aluminum flakes to create a protective layer.
- Advantages:
- Corrosion Resistance: Offers robust protection against corrosive environments.
- Dimensional Stability: Maintains the fastener’s dimensions without significant changes.
- Ease of Application: Can be applied using traditional painting or spraying techniques.
- Applications: Architectural fasteners, outdoor hardware, and infrastructure components.
Epoxy Coatings
Epoxy coatings are applied as a protective layer over metal substrates to prevent corrosion.
- Advantages:
- Durability: Highly resistant to abrasion, chemicals, and environmental degradation.
- Adhesion: Forms a strong bond with the metal surface, ensuring long-term protection.
- Versatility: Can be formulated in various colors and finishes for different applications.
- Applications: Industrial fasteners, marine hardware, and automotive components.
Special Considerations for Fastener Coatings
When selecting coatings for fasteners, you should consider how they meet specific electrical and mechanical requirements.
Addressing Electrical and Mechanical Needs
In environments where electrical conductivity is a concern, your coating choice can influence the fastener’s performance. Some coatings are non-conductive and suitable for electrically sensitive applications, while others may facilitate a necessary electrical connection. It’s key to match the coating’s properties with the electrical demands of your application.
For the mechanical needs, the coefficient of friction plays a significant role. The right coating ensures that your fasteners will have the appropriate level of grip and torque without leading to hydrogen embrittlement, which is a weakening of metal due to hydrogen exposure.
All the coatings mentioned above are designed to protect fasteners. However, the specific application and the required level of corrosion resistance determine the most suitable coating. If you still don’t know how to choose, consult with industry experts Oukailuo. Our experienced team is ready to help you select the right materials for your project. Contact us today!
Frequently Asked Questions
Which types of coatings are typically used for bolts and screws?
Bolts and screws are often coated with materials like zinc because it’s effective against corrosion and relatively low cost. You’ll find that zinc-coated fasteners work well in various settings due to their protective layer, which shields the metal from moisture and other corrosive elements.
How does PTFE coating enhance the performance of fasteners?
A PTFE coating offers a slick, non-stick surface to fasteners. This unique feature you get with PTFE coated fasteners means they’re less likely to seize up, which is particularly helpful in high-temperature applications. It also reduces friction, making it easier for you to tighten and loosen them.
What are the differences between zinc-coated and yellow chromate-coated fasteners?
Zinc-coated fasteners provide a decent level of protection against corrosion. However, adding a yellow chromate layer increases the protection, giving the fastener a longer life span. The yellow chromate coating can also offer a more distinct golden color, which might be a visual preference for certain applications.
How do coating standards affect the selection of fasteners for steel applications?
Coating standards are critical because they ensure your fasteners perform as expected. They help you see if the coating can withstand the specific environment where you plan to use them, like in steel construction, where durability and strength are paramount.