
Screws are an integral part of many mechanical devices and structures, enabling the joining and fastening of different components. However, there is more variety to screw threads than initially meets the eye. Different screw thread designs have been developed to suit diverse applications and requirements. Understanding the different types of threads is important for engineers and technicians to select the optimal thread configuration for a given task.
Screw Thread Basics
When you’re dealing with screw threads, you’re essentially looking at a helix structure designed to convert rotational to linear motion, or to fasten objects together. Understanding the basic terms will help you identify and use them effectively.
Pitch is the distance between two corresponding points on adjacent threads. It is crucial for assembly, as matching pitches ensure that the threads can engage properly.
The diameter of a screw speaks to the size of the screw. The major diameter is the largest diameter (d、D) of the thread, while the minor diameter (d1、D1) is the smallest.

The root is the bottom of the thread—between two flanks of the thread—and the crest is the top of the thread.
Let’s talk about the lead of a screw thread. If you have a single-start thread (one helix), the lead is the same as the pitch. However, for a multiple-start thread (more than one helix), the lead equals the pitch times the number of starts.
The thread angle is the angle between the flanks of the thread, which can affect the strength and load-bearing capacity. In most common screws, this angle is 60 degrees, but it can vary.
Thread System Standards

Understanding different standard threads is essential for your projects involving screws and fasteners. Let’s explore the most commonly used standards, ensuring you select the right type for your work.
Unified Thread Standard (UTS)
The Unified Thread Standard is prevalent, especially in the United States and Canada. It includes UNC (Unified National Coarse) and UNF (Unified National Fine) threads, which are designated for coarse and fine thread fasteners, respectively. These standards specify the thread form, angle, diameter, and pitch (the distance between threads).
- UNC: Commonly used where quick assembly or disassembly is needed.
- UNF: Provides higher tensile strength than coarse threads; ideal for precision applications.
- UNEF: Unified National Extra Fine
These threads can have multiple classes of fit, from loose to tight, to meet different assembly requirements. For example, 2A/2B is a common fit where 2A represents an external thread, and 2B represents an internal thread.
An adaptation of the Unified Thread Standard is the UNR thread. It includes a small and controlled rounding of the thread’s root, enhancing its fatigue resistance. This characteristic is especially crucial for applications where the screw will undergo cycles of loading and unloading.
Metric Thread Standard
The Metric Thread Standard is an internationally recognized system, characterized by its simplicity and efficiency. Metric threads are identified by their diameter (in millimeters) and pitch and come in both coarse and fine thread variants. This standard allows for easy interchanging of components globally.
- Coarse threads: Regular use when there’s no need for the fine adjustment of screws.
- Fine threads: Less likely to be cross-threaded and better for applications requiring finer tension adjustment.
British Standards
British standards include a variety of thread types, such as the British Standard Whitworth thread (BSW) and the British Association (BA) thread series. BSW is known for its specific thread angle and rounded roots and crests, giving distinct thread profiles. BA standards are often used in precision instruments and small-sized fasteners.
- BSW: A thread profile with a 55-degree thread angle, common in older or heavy machinery.
- BA: Fine threads suitable for small mechanisms, often found in electronics and model engineering.
Other Thread Standards
Aside from the major standards, there are also specialized threads such as those for pipe fittings or the American National Standard for different applications. These standards cater to specific requirements that may not be met by the more widespread categories.
- Specialty threads: Used for applications like leakproof pipe connections or environments with unique mechanical stresses.
Thread Design Variations
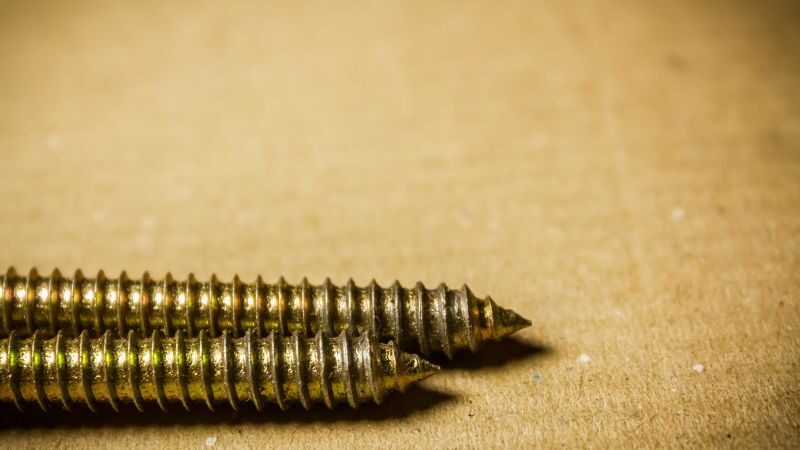
Straight vs Tapered
Straight threads maintain a consistent diameter, forming a cylinder along their length. They’re perfect for fastening where alignment and integrity against lateral forces are paramount. Whereas tapered threads narrow down like a cone as they progress, ensuring a tighter seal, commonly used in applications requiring liquid or gas containment.
Parallel vs Conical
Parallel threads are a type of straight thread where the diameter remains unchanged from one end to the other. This design allows components to screw together without changing the diameter’s relation, making them ideal for many assembly operations. Conversely, conical threads, analogous to tapered threads, decrease in diameter and are designed to create a fluid-tight seal by the thread surface itself conforming to the cone’s shape.
Left-Hand vs Right-Hand
The direction in which the thread spirals around the cylinder can either be right-hand or left-hand. A right-hand thread is more common and tightens clockwise, while a left-hand thread fastens counterclockwise. The latter is less common and might be used when the screwing action needs to counteract a force that tends to unscrew a right-hand thread, like on the left side of a bicycle pedal.
Thread Profiles and Shapes
In your journey of understanding screw threads, it’s essential to recognize the variety of thread profiles and shapes, each with specific characteristics and applications. Now let’s discuss four primary types: V-Thread, Square Thread, Acme Thread, and Buttress Thread.
V-Thread
Your experience with screws likely involves the V-thread, the most common thread profile characterized by its 60-degree angle. You’ll find these on most fastening screws and bolts. This sharp V-thread design offers good strength and is easy to manufacture, making it suitable for a majority of general assembly tasks.
Square Thread
Square threads are distinguished by their square-shaped threads, with the flank perpendicular to the screw axis. These threads are designed for power transmission, reducing friction compared to V-threads. You’ll typically see them in jacks, vises, and other mechanisms where efficient motion is needed.
Acme Thread
The Acme thread profile stands out with its trapezoidal shape, providing a compromise between the strength of a V-thread and the low friction of square threads. Its 29-degree flank angle makes it more robust and suitable for heavy loads often found in lead screws and vise mechanisms.
Buttress Thread
Lastly, Buttress threads have a triangular profile with one vertical flank and one angled flank. This design allows for high force transmission in one direction while maintaining free motion in the other — common in applications like screw jacks and presses where unidirectional load is present.
Thread Mechanics and Dynamics
In the realm of screw threads, understanding the interplay of forces and the resulting motion is crucial. You’ll find that the torque applied and the resulting force are pivotal for the function of threads as both a simple machine and a component in bearing systems.
Torque and Force
When you apply torque to a screw, you’re essentially twisting it to generate linear motion. This torque is calculated as the force exerted at a distance from the pivot point, which is the mean radius of the screw. The equation M = Wr tan(ϕs + α) represents the moment or torque needed to overcome friction and generate movement, where:
- M is the moment or torque.
- W is the linear force applied on the screw.
- r is the mean radius of the screw.
- ϕs is the screw friction angle.
- α is the screw thread pitch angle.
This linear force, or the load on the screw, translates into the rotary motion needed to raise or lower the screw, showcasing the principle of mechanical advantage in simple machines.
Friction and Wear
Friction plays a significant role in the dynamics of screw threads. It’s the resistance that one surface or material encounters when moving over another. Here’s how it factors in:
- Friction Angle (ϕs): This angle contributes to the understanding of how much torque is needed for the screw to start moving. Higher friction means more torque is required.
- Wear and Tear: Continuous interaction between threads can lead to wear, affecting both efficiency and the service life of the screw.
To minimize wear and prolong the life of screw threads:
- Lubrication: Apply suitable lubricants to reduce direct metal-to-metal contact.
- Material Selection: Use materials that have high wear resistance for threads.
Remember, the better you manage friction through lubrication and material choice, the smoother the translation from rotary to linear movement will be, maximizing the mechanical advantage of your screw threads.
Thread Measurement and Tools
To achieve precision in your projects involving threaded fasteners, it’s crucial to measure threads accurately. The thread pitch diameter and effective diameter play a significant role in this process. Here’s how you can measure these dimensions effectively using specific tools.
Micrometers and Gauges
Micrometers function as a precision measuring instrument that you use to obtain the accurate diameter of male threads. The tool works by measuring the pitch diameter, which is the diameter of an imaginary cylinder where the thread’s width and space between threads are equal. Generally, you’ll find micrometers measuring in fine increments, allowing you to reach a high degree of precision.
- Pitch Micrometer: particularly designed to measure the pitch diameter of screw threads.
- Thread Gauges: essential for identifying the profile of threads on a threaded fastener. They help you to verify the pitch or the number of threads per inch by matching the teeth with the threads.
Type | Function |
---|---|
Micrometer | Measures the effective diameter of male threads |
Thread pitch gauge | Helps identify the number of threads per inch (TPI) |
Lathes and Machinery
Similarly crucial are Lathes and other machines, which serve a dual purpose. Not only can they create the threads by cutting, but some also have the capability of measuring the threads they’ve produced. They are particularly used for manufacturing both male and female threads, considering their basic profile. Additionally, many modern lathes come equipped with digital readouts to give you precise measurements.
By utilizing micrometers, gauges, and machining equipment, you can precisely measure and create threads that match your project’s specifications.
Special Thread Forms
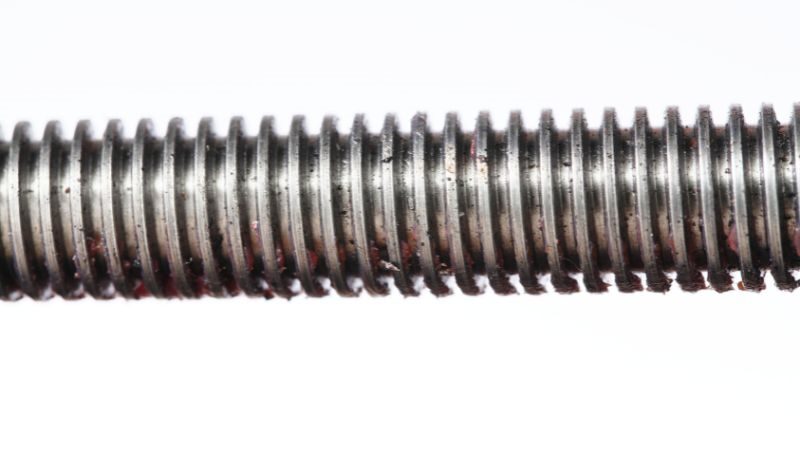
In the world of threading, special thread forms serve precise purposes. You’ll encounter unique designs tailored for secure connections and high-strength applications. Let’s explore some specialized threads that you might use in your projects.
Pipe Threads
You’ll often deal with pipe threads when you’re working on plumbing or fluid handling systems. These threads are designed to provide a leak-proof seal and usually have a taper to create a tighter fit as you screw them closer. The most common standards for these threads are the NPT (National Pipe Taper) and BSPT (British Standard Pipe Taper). They each have different thread angles and diameters which make them suitable for specific uses.
- NPT Threads: Common in North America, they seal tightly due to their tapered profile.
NPT Thread Size | Outside Diameter | TPI |
---|---|---|
1/8″ NPT | 0.405″ | 27 |
1/4″ NPT | 0.540″ | 18 |
3/8″ NPT | 0.675″ | 18 |
1/2″ NPT | 0.840″ | 14 |
3/4″ NPT | 1.050″ | 14 |
- BSPT Threads: Predominately used in Europe and Asia, they also have a tapered form for sealing fluids.
BSP Thread Size | Outside Diameter | TPI |
---|---|---|
1/16 Inch BSP | 7.7 mm / 0.304′′ | 28 |
1/8 Inch BSP | 9.7 mm / 0.383′′ | 28 |
1/4 Inch BSP | 13.16 mm / 0.518′′ | 19 |
3/8 Inch BSP | 16.66 mm / 0.656′′ | 19 |
1/2 Inch BSP | 20.99 mm / 0.825′′ | 14 |
5/8 Inch BSP | 22.99 mm / 0.902′′ | 14 |
The root radius, a design feature of some thread forms, impacts the thread’s strength. It’s the small curve at the bottom of the thread groove which can absorb stress and reduce the possibility of cracking under loads.
Thread Handling and Use
When dealing with screw threads, it’s crucial to understand the specifics of fastening and the levels of engagement between male and female threads. Proper technique ensures longevity and reliability in threaded connections.
Fastening and Securing
Fastening is the process of joining objects using a bolt, screw, or similar types of fasteners. Here’s how you can do it correctly:
- Select the right fastener: Match male (bolt or screw) threads to the appropriate female (nut or tapped hole) threads.
- Align accurately: Begin by hand to prevent cross-threading.
- Tighten appropriately: Use the correct tool to tighten fasteners; over-tightening can strip threads, while under-tightening may lead to a loose joint.
The term jack screw refers to a type of screw used in electronics to provide spacing or to secure components like connectors. The use of a split nut, which is divided into two pieces to wrap around the shaft without having to thread the end, can facilitate repairs where disassembly is difficult.
Thread Engagement
Thread engagement refers to the depth that male threads interlock with female threads. To achieve proper engagement:
- Ensure depth: Typically, the depth of engagement should be at least equal to the diameter of the screw or bolt.
- Check thread quality: Damaged or dirty threads can compromise thread engagement.
Engagement Feature | Detail |
---|---|
Minimum Engagement | Equal to the fastener’s diameter |
Thread Condition | Must be clean and undamaged |
Engagement Check | Verify visually and through manual feel |
The snugness of the fit between threads is critical. You should be able to feel resistance as you tighten, indicating that the threads are in full contact. Be mindful not to strip threads by forceful over-tightening.
In conclusion, there are several common types of screw threads used for different purposes based on factors like mechanical stresses, manufacturing constraints, and required precision. Metric and unified threads are most prevalent for general mechanical assembly. Specialized thread forms like buttress, Acme, and square threads address needs in areas like heavy machinery, linear motion, and high-strength joints.
For readable, here is a concise form:
Thread Type | Key Features |
---|---|
Standard Threads | Increased minor pitch diameter and shaft strength; Higher strength; Increased linear force for equal torque; Reduced linear actuation per rotation; Accepted standardized dimensions |
Square Threads | Lower number of threads per axial distance; Increased clamping speed; Low friction; High power transfer efficiency; Reduced minor pitch diameter and strength; Difficult to manufacture |
ACME Threads | Trapezoidal thread form; High load capacity; High efficiency in power transmission; Used in vises, jacks, clamps, leadscrews |
Buttress Threads | Angled pressure flank; Withstand heavy axial loads; Prevent loosening from vibration or thermal expansion/contraction; Used in vises, C-clamps, jacks |
Sharp V Threads | Hard to produce; Easily damaged; Single cutting tool can produce various pitches |
Unified Threads | Common thread form in the US; Several unified thread series |
The thread angle, pitch, and profile all influence the thread’s performance. Selecting the proper thread type maximizes functionality while preventing failure. As mechanical systems continue advancing, new thread designs may also emerge. Overall, applying thread engineering principles helps ensure components are reliably fastened for their intended uses.