When it comes to fastening objects, you may often find yourself wondering whether to use a bolt or a screw. While they may look similar, there are key differences between these two types of fasteners that affect their usage in various applications. This article aims to clarify these distinctions and help you determine when to choose one over the other.
Defining Bolts and Screws
Bolts typically have a flat, unthreaded shank followed by threaded sections. Their heads can be hexagonal, square, or even round with a slot or hole for driving. On the other hand, screws have a fully threaded shank and various head styles, such as flathead, pan head, or countersunk. The primary difference in function is that bolts are used with unthreaded objects and nuts, while screws join objects with pre-cut threads.
Here’s a quick comparison for clarity:
Bolts | Screws | |
---|---|---|
Shank | Unthreaded | Fully Threaded |
Heads | Hexagonal, Square, Round | Flathead, Pan Head, Countersunk |
Primary Function | Secure with a Nut | Join Objects with Pre-Cut Threads |
Mechanics of Bolts

Bolted Joints
The main components of a typical bolted joint are:
- Bolt: A threaded fastener with a head.
- Nut: A threaded component that mates with the bolt.
- Washer: A thin, flat piece of metal used to distribute the load of the bolt and nut.
The purpose of a bolted joint is to clamp parts together using a force generated by the tightening of the nut. Your main goal in creating a sturdy joint is to ensure the bolt has been tightly fastened, allowing the components to stay securely in place.
Types of Bolts
There are several types of bolts, each with their specific applications and designs. Some common types of bolts include:
- Hex bolts: These are general-purpose bolts that have a hexagonal-shaped head. They are commonly used in various industries such as construction and automotive.
- Anchor bolts: Anchor bolts are designed to secure objects to concrete. They are commonly found in heavy-duty projects like building foundations.
- L-bolts: L-bolts have an L-shaped design and are used for attaching objects to concrete or masonry surfaces.
- J-bolts: These bolts have a J-shaped design and are used for hanging objects or securing them to a surface.
- Shoulder bolts: Shoulder bolts have a smooth, unthreaded shank between the head and threads, which allows for precise spacing and rotation.
- U-bolts: U-bolts have a U-shaped design and are typically used for securing pipes or other round objects to a surface.
Mechanics of Screws
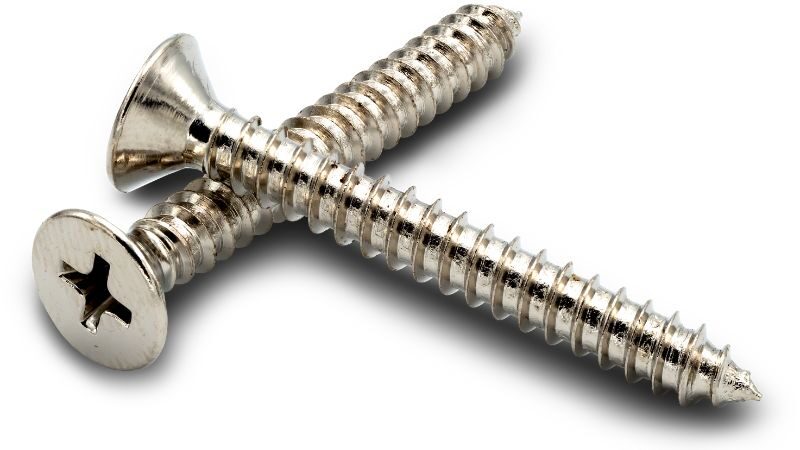
In this section, we’ll explore the thread patterns, uses, and types of screws to give you a clearer understanding of their mechanics.
Thread Patterns and Uses
Thread patterns on screws determine their specific uses. Throughout the manufacturing of screws, you’ll find various thread designs serving different functions. Some common thread patterns and their uses include:
- Wood screws: The coarse threads are designed for use in wooden materials. They provide a strong grip and hold the pieces together tightly.
- Sheet metal screws: With sharp threads, these screws make their own threads in sheet metal applications, ensuring a tight and secure hold.
- Machine screws: These screws have finer threads and are generally used with pre-threaded holes in metal, plastic, or other materials.
Types of Screws
Various screw types cater to different applications and materials. Some common screw types are:
- Self-tapping screws (drywall screws, sheet metal screws): These screws create their threads as they are driven into the material. They are often used in situations where the material does not have any pre-threaded holes available.
- Machine screws: As mentioned earlier, these screws work best with pre-threaded holes in metal, plastic, or other materials. They come in a wide range of head shapes and drives to accommodate various needs.
- Dowel screws: With threads at both ends, dowel screws are used to connect two separate pieces of wood without the need for visible screw heads.
- Carriage bolts: Although not the same as screws, carriage bolts share some similarities. Both have external threads and a flat or round head. However, bolts need nuts and lock washers to secure them firmly.
Comparing Bolts and Screws in Details

Installation and Tools
When you’re working on a project, it’s essential to choose the right type of fastener. Let’s compare the installation process and tools required for bolts and screws.
For bolts, you typically need to drill a hole through the materials you are joining. Then, you insert the bolt through the hole and secure it with a nut on the opposite side. The use of a washer is common to help distribute load evenly and increase the holding power of the joint. The tools you may need for installing bolts include a drill, a set of wrenches, or a socket set.
On the other hand, screws are designed to cut their own threads into the material, as they are being driven in. This means screws don’t require nuts or drilled holes with pre-cut threads like bolts do. Instead, you might need to pre-drill a smaller diameter hole (called a pilot hole) for the screw. When it comes to tools, you usually need a screwdriver or a power drill with appropriate driver bits for screw installation.
Tensile and Shear Strength
It’s crucial to consider the tensile and shear strength of these fasteners when selecting between bolts and screws for your project, as they impact the overall load-bearing capacity and durability.
Bolts generally have a higher tensile strength, which means they can withstand a larger pulling force along their axis. The presence of a washer and a nut helps to distribute the load more evenly, leading to a stronger connection. Bolts are preferred in heavy-duty applications like construction, automotive, and machinery, where stability is crucial.
In terms of shear strength, screws can be a better choice for some applications. The continuous thread engagement between the screw and materials, along with the pulling force generated by screw’s torque, creates a close and secure hold. This is ideal for joining materials like wood, metal, or plastic, where a tight bond is desired.
To sum it up, the main differences between bolts and screws lie in the installation process, tools required, and their performance in terms of tensile and shear strength. Make sure you consider these factors when choosing the appropriate fastener for your project.
Specialized Applications

Bolts and Structural Integrity
In construction projects, you will often encounter the use of bolts for ensuring structural integrity. A common type of bolt for such applications is the anchor bolt. Anchor bolts are typically made of steel and are used to secure structures like beams and columns to concrete foundations. The purpose of these bolts is to create a strong, stable joint that can withstand forces and load without compromising the structural integrity.
Some examples where you might use bolts for structural integrity include:
- Attaching beams to columns in steel-framed buildings
- Securing heavy equipment to concrete slabs
- Anchoring support structures for bridges
Screws in Woodworking
On the other hand, screws are more popular in woodworking applications. They are versatile and commonly used to fasten various types of wood materials such as plywood, deck planks, framing, and beams. While working on woodworking projects, you may encounter different types of screws suitable for specific tasks.
For instance:
- Deck screws are designed to resist corrosion and have a special thread for securing deck planks without splitting the wood.
- Wood screws are specifically made for wood-to-wood connections and have a sharp point for easy penetration and a smooth shank to draw the two pieces of wood together.
- Sheet metal screws come in handy when you need to attach thin pieces of metal to wood or plywood.
When using screws in woodworking, ensure proper repairs are made when signs of wear or damage are evident. This will help maintain the strength and durability of your projects.
Selection Criteria
Size and Length Considerations
When selecting bolts and screws for your projects, it’s essential to consider the size and length that best suit your needs. The size refers to the diameter of the bolt or screw’s shank, while the length is the distance from the head to the threaded end. Common sizes include metric (M) and standard (inch) systems, such as M8 or 5/16″.
To determine the appropriate size and length, start by measuring the thickness of the materials you plan to join. When it comes to length, opt for a fastener that extends beyond the material by at least one thread. You should also account for the space needed for washers and nuts.
Here’s a simple reference table for choosing sizes:
Material Thickness | Recommended Bolt Size | Recommended Length |
---|---|---|
1-2mm | M5 | 10-14mm |
2-4mm | M6 | 14-20mm |
4-6mm | M8 | 20-30mm |
6-10mm | M10 | 30-45mm |
Material and Cost Efficiency
Bolts and screws come in various materials, each with its advantages and cost implications. Some of the most common materials include:
- Stainless steel: This is a popular and versatile choice, as it resists corrosion and has excellent strength. It’s ideal for applications exposed to water, chemicals, or extreme temperatures.
- Brass: Known for its corrosion resistance and decorative appeal, brass is a good choice for outdoor or decorative projects. Keep in mind that it’s not as strong as stainless steel, so avoid using it in load-bearing applications.
- Bronze: Similar to brass, bronze offers excellent corrosion resistance and is suitable for outdoor and marine environments. It’s often used for its decorative appearance and antique feel.
- Nylon: This lightweight, non-conductive, and corrosion-resistant material is ideal for electrical or low-stress applications. Nylon fasteners are also a budget-friendly option.
To help you decide which fastener is best suited for your needs, consider the following table:
Criteria | Bolt | Screw |
---|---|---|
Material | Metal, plastic | Metal, plastic |
Corrosion Resistance | Good (with stainless steel) | Good (with stainless steel) |
Ease of Installation | Moderate | Easy |
Ease of Replacement | Moderate | Easy |
Disassembly & Reassembly | Adjustable, secure connection | Simplified, no additional hardware is needed |
Keep these factors in mind when working on your projects, and you’ll be able to maintain a durable and reliable connection with the appropriate choice of fasteners.
In addition, when it comes to maintenance and durability, the material of the fasteners plays a crucial role. Stainless steel is a popular choice for both bolts and screws due to its corrosion-resistant properties. This ensures that your fasteners remain strong and reliable over time, effectively reducing maintenance needs. In addition, stainless steel also provides a degree of visual appeal, making it suitable for applications where aesthetics matter.
Industry Standards and Manufacturing
When it comes to the world of fasteners, understanding industry standards and manufacturing processes is crucial for ensuring the quality and compatibility of your chosen bolts and screws. In this section, we’ll dive into regulatory compliance and explore global manufacturing variations that impact the products available to you.
Regulatory Compliance
As a user of fasteners, it’s essential to be aware of the various regulatory standards and specifications that guide the production and usage of bolts and screws. These regulations ensure the quality, safety, and consistency of fasteners across various applications and industries. Some common standards that you’ll encounter include:
- ISO (International Organization for Standardization): A set of international standards that covers a wide range of industries and products, including fasteners.
- ANSI (American National Standards Institute): A private organization that oversees the development of national standards in the United States.
- ASTM (American Society for Testing and Materials): A globally recognized organization that develops and publishes technical standards, including those for fasteners.
- DIN (German Institute for Standardization): Develops standards for various German industries, with their dimensional specifications being commonly used globally for fasteners.
Global Manufacturing Variations
Different manufacturing companies around the world have their unique production processes and material preferences. For instance, stainless steel is a popular choice for bolts and screws due to its corrosion resistance, strength, and durability. However, some manufacturers may offer a wider range of materials, including other metals and plastic, to cater to specific applications or industries.
From region to region, there may be differences in dimensions, thread patterns, and head types. Coarse and fine thread options, for example, vary among metric bolts depending on the region. Additionally, head shapes and drives can range from Phillips and Torx to square, slotted, and hexagonal. To ensure compatibility in your project, it’s crucial to verify the specifications of the fasteners you need and match them with products from reputable manufacturers.
In summary, bolts and screws serve similar purposes of joining and fastening objects together, but they have key differences in their design and usage. Bolts are larger and sturdier than screws, with threads along their entire length. This allows bolts to handle greater tensile and shear forces when used with nuts. Screws, on the other hand, have threads only on the tip and are designed more for embedding into softer materials like wood.
While both bolts and screws can be used to assemble parts, bolts are better suited for applications involving heavy loads or vibration. Their two-piece assembly with nuts makes bolts easier to tighten and loosen as needed for maintenance. Screws are better for lightweight joining of softer materials where the threads can grip directly.
Knowing these differences in size, threading, strength and intended usage allows one to choose the right fastener for the job.