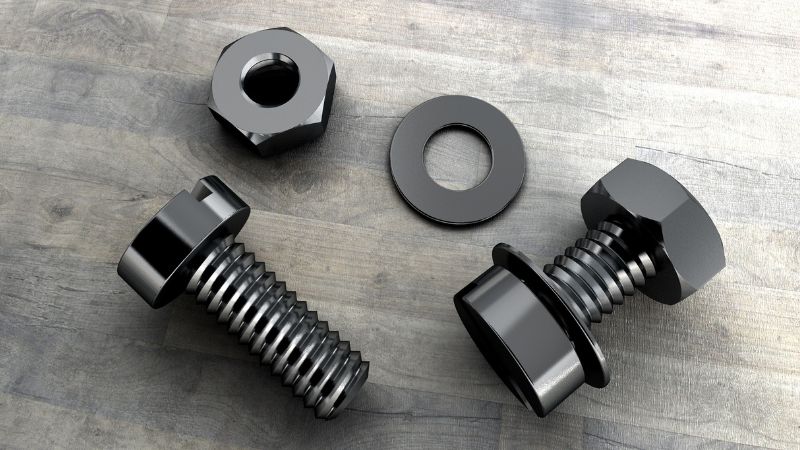
What is Cold Heading?
Cold heading is a method where you can shape metal into parts without cutting away any material. It’s a way to make things like screws and bolts quickly while saving on metal.
Because the process can create complex shapes efficiently, it’s also used to produce specialty parts and components across various industries.
Why Choose Cold Heading?
- Less Material Waste: Cold heading reformats material without removal, maximizing raw material use and reducing waste, saving you money.
- Energy Savings: Cold forming requires no heat, using significantly less energy than hot forging, leading to lower production costs.
- Increased Precision: Cold heading tools create parts with high precision, ensuring consistency to meet your exact specifications.
- Stronger Parts: The room temperature shaping in cold forming enhances the material’s strength through work hardening, resulting in more durable parts.
- Speed: Cold heading machines can produce thousands of parts per hour, often faster than traditional machining methods.
What are the Cold Heading Process?
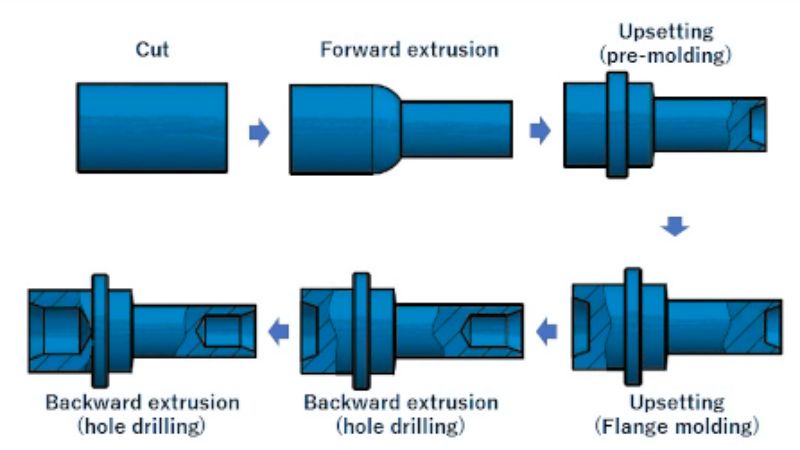
Slug Preparation
First off, you need to start with a ‘slug’, which is just a cut piece of metal wire. It’s very important to choose good quality metal that fits what you’re making. Different metals like steel or brass can be used. Your slug has to be the right length and size for the part you want to make. Once it’s cut, it’s ready for the next step.
Upsetting Process
The upsetting process squashes your slug between a die and a punch. The die is like a mold, and the punch is a hammer that shapes your metal. As you press the metal, it starts to flow and fill the die, taking on its shape. This is called an ‘upset’. By doing this, you make the basic form of your part.
Pointing and Extrusion
Pointing is you making one end of the slug sharp. This helps it fit into the die better for the next part. Extrusion is where you push the metal through a die to add detailed shapes or to make holes, like in the middle of a screw. The metal moves like clay and is formed into the intricate parts you need. There’s no wasted metal, and you end up with a precise, strong component ready for use.
Machine Technology and Automation in Cold Heading
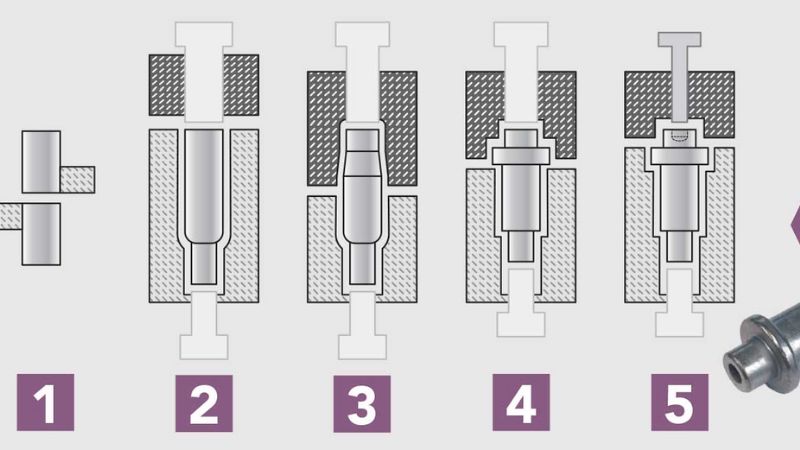
Types of Cold Heading Machines
Cold heading machines are specialized pieces of equipment designed to shape metal by applying force without generating heat. You’ll commonly encounter two types of machines: cold-headers and part formers.
- Cold-headers are perfect for simple projects. These machines generally perform a single punch or forge on a piece of metal to create a specific shape.
- Part formers are more sophisticated and suited for complex parts. These machines can have multiple dies and make several progressive moves to form intricate shapes with good dimensional tolerances.
Transfer Mechanisms in Automation
Your cold heading machine likely includes an automated transfer mechanism. This mechanism automates the movement of parts from one station to another during the heading process.
- Linear transfer is effective for short distances and can be quite speedy.
- Rotary transfer moves parts around a circular path, which can be more suitable for complex assemblies and longer processing paths.
Metals Used in Cold Heading
Material | Characteristics | Common Applications |
---|---|---|
Steel | Most common material; strength and durability | Fasteners, structural components |
Aluminum | Lightweight, corrosion-resistant | Weight-sensitive applications |
Brass | Copper-zinc alloy; good machinability, corrosion resistance | Electrical components, decorative items |
Copper | Excellent conductivity | Electrical applications, plumbing fittings |
Nickel Alloys | High strength, heat and corrosion resistance | Specialized applications |
Titanium | High strength-to-weight ratio, corrosion resistance; more expensive | Aerospace, medical applications |
How do different materials affect the outcome of the cold heading process?
The type of material you use in cold heading can influence both the tooling longevity and the final product. Materials such as steel, aluminum, and copper vary in ductility and strength, which can affect the cold heading process.
High ductility materials are preferred because they can deform without cracking. The chemical composition affects strength and formability, impacting how the material behaves during heading. A fine grain structure typically results in better mechanical properties, while a coarse structure may lead to poorer performance. Temperature sensitivity is also important, as some materials can become brittle at lower temperatures.
Applications of Cold Heading
Industry | Application | Importance of Cold-Headed Fasteners |
---|---|---|
Automotive Industry | Engine Components | Must withstand high temperatures and stress. |
Chassis | Ensures the vehicle frame remains secure. | |
Wheels | Keeps tires tightly fastened. | |
Electronics Manufacturing | Circuit Boards | Provides secure connections. |
Devices (e.g., smartphones, laptops) | Allows for compact and reliable assembly. | |
Construction Sector | Building Frameworks | Bolts form the backbone of structures. |
Infrastructure (e.g., bridges, tunnels) | Safety depends on the integrity of cold-headed fasteners. |
At Oukailuo, we are committed to merging advanced technology with outstanding craftsmanship to create solutions that excel in performance.
Visit our website to explore our diverse range of products and see how we can assist you in elevating your project. Thank you for choosing Oukailuo—where quality and innovation come together!
Frequently Asked Questions
Can you explain the basic steps involved in a cold heading operation?
Sure! The process starts with cutting wire to the desired length. Next, the wire is fed into a machine and hit with high pressure by a series of dies and punches. Each strike shapes the wire into a part, like a bolt head. The final product often goes through additional processing like threading or coating.
What is the typical range of sizes for machines used in cold heading?
Cold heading machines come in various sizes to handle different wire diameters and lengths. Smaller machines might work with wire that’s just a few millimeters thick, while larger equipment can handle wire that’s several centimeters in diameter. The size of the machine depends on the end product needed.
How has automation impacted the cold heading industry in recent years?
Automation has reshaped the cold heading industry by improving precision and output. Automated machines can produce fasteners and components at a faster rate, with consistent quality and fewer errors. This has allowed for more complex designs and has increased productivity in manufacturing facilities.