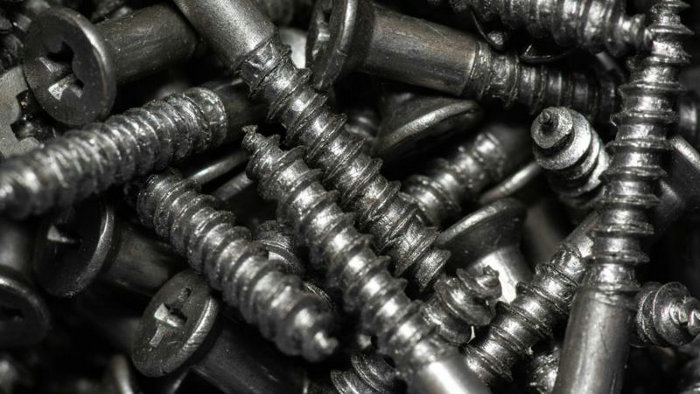
Screws are essential components in countless construction and assembly projects, like wood screws and machine screws; they serve as a simple yet sophisticated means of holding materials together firmly. Typically, screws are crafted from a variety of metals, each selected for their particular properties that suit different uses and environments. The most common materials used for screws include steel—which is often carbon steel for added strength—stainless steel, brass, aluminum, and sometimes specialized alloys for specific applications.
When selecting the right screw for your project, considering the properties of the material is crucial—whether it requires a certain level of tensile strength, shear strength, or needs to withstand environmental challenges like humidity, chemicals, or temperature fluctuations.
In this article, we will discuss the material used to make screws.
The Type of Screw Materials
As you explore the world of screws, you’ll find they are made from a variety of metals and non-metallic materials, each selected for its unique properties to suit different applications.
Common Metals for Screws
- Steel: A workhorse of the industry, steel screws are affordable and robust. They are often made from carbon steel which provides the necessary hardness.
- Stainless Steel: With added chromium, stainless steel screws resist corrosion and are suitable for applications where durability is key.
- Brass: Your brass screws offer aesthetic appeal with added corrosion resistance, commonly used in decorative applications.
- Copper: When you need extra corrosion resistance, copper screws are reliable, though they come at a higher cost.
- Aluminum: You’ll find aluminum screws lighter in weight and resistant to corrosion; they are favored in applications where weight is a concern.
- Titanium: For the highest strength-to-weight ratio, titanium screws are your go-to, though they are more expensive than other metals.
Non-metallic Materials
Screws are not limited to metals; some are made from robust non-metallic options:
- Plastic: Lightweight and corrosion-resistant, plastic screws are useful in electrical applications and where metal screws would cause interference.
- Aluminum Alloy: This material combines aluminum with other elements to enhance properties like strength and corrosion resistance, expanding the range of applications for aluminum screws.
Each material offers distinct benefits, and your choice will largely depend on the specific requirements of your project, such as strength needed, exposure to elements, and whether conductivity is a factor.
Here is a quick view of the composition and benefits of some common screw materials.
Material | Composition | Benefits | Use Cases |
---|---|---|---|
Steel | Carbon steel – iron and carbon | Sturdy, durable | Indoor applications like furniture |
Stainless Steel | At least 10.5% chromium | Rust-resistant | Outdoor construction, high moisture areas |
Brass | Copper and zinc alloy | Corrosion resistant, decorative | Visible applications like instruments and furnishings |
Titanium | Titanium alloys | Very strong, lightweight, corrosion resistant | Aerospace, medical devices |
Copper | Mostly copper | Conducts electricity, corrosion resistant | Electrical fittings, plumbing |
Polymer/Plastic | Nylon, polycarbonate | Chemically resistant, non-conductive | Automotive, electronics |
Material Properties
In exploring the various materials that make up screws, you’ll find a combination of durability, corrosion resistance, and strength considerations shaping your choices.
Metal Attributes
When you select screws, the metal’s attributes, such as melting point, durability, and conductivity, are crucial. Stainless steel, particularly 316 grade, is known for its excellent corrosion resistance and durability, making it suitable for use in harsh or marine environments. For instance, 316 stainless steel contains molybdenum, which improves its resistance against chlorides. On the other hand, a metal like aluminum is appreciated for its lightweight and non-corrosive properties, though it has a lower melting point and strength compared to steel.
Material Grades
Material grades give you an insight into the specific characteristics and performance you can expect from your screws. The grades are identifiers that tell you about the alloy’s composition, strength, and corrosion resistance.
- Alloy Steel: Known for high strength and is often graded with numbers like 8.8, 10.9, and 12.9.
- Stainless Steel: Comes in grades like 304, 316, and 410.
- 304: A common choice for general use.
- 316: Offers enhanced corrosion resistance, used in marine applications.
- 410: A hardened stainless steel with high strength and mild corrosion resistance.
The grade 410 stainless steel is often brought up when you need extra hardness and wear resistance, while 316 is your friend in fighting against corrosion, especially in salty environments. It’s the addition of elements like carbon, chromium, and nickel in various amounts that create different grades and affect properties such as strength and corrosion resistance. Consider the stainless steel grade alongside factors like the environment and stress the screw must endure to ensure you choose the right one for your needs.
Material Quality
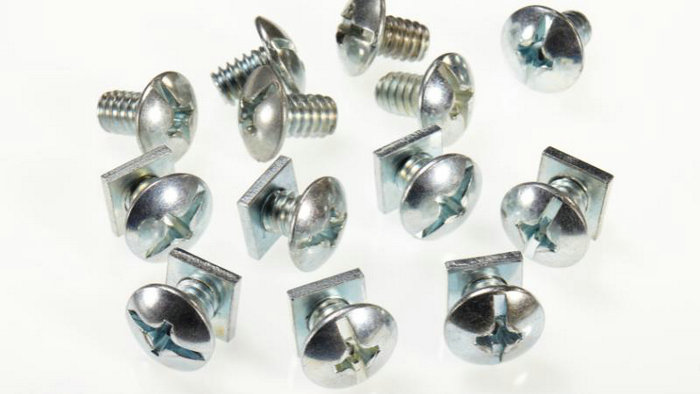
When picking out screws for your projects, it’s important to consider their material qualities, which influence how they’ll perform in different environments. Here’s a breakdown to help you understand what you’re working with.
Strength: Your heavy-duty tasks call for strong screws, and that’s when steel or titanium take the stage. They’re designed to handle the pressure, so you don’t have to worry about them giving in when it counts. On the flip side, brass and aluminum, while still solid options, are best saved for lighter-duty jobs.
Corrosion Resistance: Hate rust? Stainless steel, brass, and certain plastics say “No way!” to corrosion, keeping things pristine. Stainless steel is a champ outdoors, especially near the coast. If steel is your only option, consider a protective finish to keep the dreaded rust at bay.
Weight: If lighter loads are a must, like in the fast-paced world of racing or gravity-defying aerospace engineering, aluminum and titanium are your go-to lightweights. They bring strength without the bulk, keeping everything streamlined and efficient.
Conductivity: For your electrical needs, copper’s conductivity is unmatched, which is why it’s often found in wiring applications. And if you’re looking to avoid a current, plastic screws are your perfect insulator, ensuring that electricity stays where it should.
Here’s a quick reference table to sum things up:
Material | Strength | Corrosion Resistance | Weight | Conductivity |
---|---|---|---|---|
Steel | High | Low* | Medium | Low |
Stainless Steel | Medium | High | Medium | Low |
Brass | Medium | High | Medium | Good |
Aluminum | Low | High | Low | Good |
Titanium | High | High | Low | Low |
Copper | Low | High | High | Excellent |
Plastic | Low | High | Low | None |
*Can be improved with coatings.
Remember, your projects deserve the right kind of strength, protection against the elements, a manageable weight, and the right conductive properties. By matching the material qualities to your needs, you’re setting yourself up for success.
Coatings and Finishes
When you select screws for your project, understanding the importance of coatings and finishes can greatly influence the durability and effectiveness of the fastener. Here’s what you need to know.
Surface Treatments
Zinc plating is the most frequent treatment you’ll encounter due to its balance of good rust resistance and affordability. The process of galvanizing involves applying a zinc coating to steel or iron to prevent corrosion. For a more aesthetically pleasing finish, chrome plating layers chromium over the fastener, offering enhanced corrosion resistance and a shiny surface. If you require even more protection against wear and tear, ceramic-coated screws offer an advanced layer of defense, particularly suitable in harsh environments.
- Zinc Coating: Common and cost-effective, provides decent protection against corrosion.
- Nickel Plating: Offers a balance of durability and decorative appeal.
- Chromium: Known for hardness and an impressive shine.
- Ceramic Coating: Ceramic layers serve as a barrier against high temperature and chemical exposure.
Coating Benefits
Your screws’ longevity and performance are directly linked to their finish. A capable coating like zinc or ceramic not only guards against corrosion but can also provide a lubricating feature, which makes the installation process easier. Moreover, certain coatings are aesthetically pleasing—nickel and chromium offer a sleek silver finish that may complement your project’s visual design.
- Corrosion Resistance: Essential for outdoor or moisture-prone environments.
- Aesthetic Appeal: Finishes like nickel and chrome are visually appealing and can add to the design.
- Ease of Use: Some coatings reduce friction, making screws easier to install.
By choosing the appropriate coating or plating, you ensure your screws perform their best for the longest time.
Resistance to Elements

When selecting screws for your project, understanding their resistance to various elements is crucial. This will ensure the longevity and durability of both the screw and the application it’s used in.
Corrosion Resistance
Stainless steel screws are highly resistant to corrosion due to the addition of chromium to the alloy. Galvanized screws, which are steel screws coated with a layer of zinc, also provide enhanced corrosion resistance. This zinc coating forms a barrier that prevents moisture and oxygen from reaching the steel. However, if the galvanized coating is damaged, it can lead to rust.
For applications in marine environments, silicon bronze screws are excellent choices due to their high resistance to corrosion from salt water. Silicon bronze is an alloy made from copper, silicon, and other metals, offering superior longevity in harsh conditions.
Use in Various Environments
Material | Properties | Ideal Environments |
---|---|---|
Stainless Steel | Durable, resists corrosion | Outdoor, humidity, light marine exposure |
Galvanized | Zinc coating, budget-friendly | Outdoor, less corrosive environments |
Silicon Bronze | Exceptional corrosion resistance | Marine, high-salinity areas |
For general outdoor use, both stainless steel and galvanized screws are suitable; stainless steel offers a balance between cost and performance for many environments. In contrast, silicon bronze screws are your best bet for severe exposure, especially where the presence of salt or other corrosive elements is a concern. Remember to consider the specific conditions your screws will face to select the most appropriate type for your needs.
Screw Manufacturing Process
When you think about screws, you might take their presence for granted, but the manufacturing process is intricate and essential for producing the durable fasteners you use in everyday applications.
Manufacturing Processes
Cold Heading is a key method where the wire is cut to a specified length, and then the head is formed at room temperature. This process is efficient and cost-effective, ensuring the screw’s head is perfectly shaped to accommodate the driver. Thread Rolling follows, where the threads are formed on the screw. This is performed under high pressure between two dies: Reciprocating Die, where one die moves back and forth, and Planetary Die, with several dies moving around the screw. This process not only shapes the threads but also hardens them for increased strength.
Cold Forming techniques involve altering the shape and size of metal pieces without the addition of heat. Your screws often undergo this process to achieve the precise dimensions and durability required for their intended use. By utilizing the Cold Forming method, the structure of the metal becomes denser at the thread crests and roots, which subsequently enhances the screw’s overall strength.
Screw Heads and Threads
In exploring the design of screws, you’ll gain an understanding of how different head styles and thread types suit various applications.
Understanding The Screw Heads
Your project’s success can hinge on selecting the right screw head. Here are a few common styles:
- Flathead: This screw head is conical with a flat outer face and tapering inner face, allowing the screw to sit flush with the surface.
- Oval: These screws have an oval-shaped top surface and are designed to sit flush on the surface of the material they are screwed into. They require a countersunk hole and provide an unobtrusive appearance thanks to their low profile.
- Blinding: These screws, also known as binding head screws, have a domed head with angled sides to provide a smooth finish. The angled underside of the head binds the screw tightly to the surface it is screwed into.
- Pan: Pan head screws have a flat top surface with sloping sides. They do not require a countersunk hole like oval heads, and the large bearing surface underneath the head provides good clamping force without damaging soft materials. Pan heads are very versatile since they can be used with or without countersinking.
Understanding The Thread Types
The thread of a screw is its defining feature, and threads come in two dominant types according to Metric Thread Standard:
- Coarse Threads: With wider spacing, they’re designed for quicker driving and better grip in soft materials.
- Fine Threads: These threads are closer together, providing finer adjustments and stronger holds in hard materials
Here are 4 common types of screw threads:
- V-Thread: The most common thread profile, V-threads have a 60-degree angle suitable for general fastening applications.
- Square Thread: Square threads have perpendicular flanks designed to reduce friction for power transmission.
- Acme Thread: Acme threads are trapezoidal, balancing strength and lower friction – suitable for lead screws and heavy loads.
- Buttress Thread: Buttress threads have one vertical, one angled flank for high force in one direction but free motion in the other.
Tools and Accessories
Before diving into your project, it’s important to equip yourself with the right tools and accessories to handle screws efficiently. The right gear will make the job smoother and help ensure a secure and proper fit.
Required Tools for Screw Use
Screwdrivers: Without a doubt, your toolkit should include a good set of screwdrivers. Depending on the screw head, you’ll need the correct type. Here are the essentials:
- Flat-head Screwdriver: Ideal for screws with a single slot.
- Phillips Screwdriver: Has a cross-shaped tip, suitable for screws with a cross slot.
- Hex Screwdriver: For screws with a hexagonal recess.
Drills: If you’re working with a lot of screws or tougher materials, a power drill will save you time and effort.
- Cordless Drill: For ease of use and maneuverability.
- Drill Bits: A set that matches various screw sizes and head shapes.
Remember, always choose the right size of screwdriver or drill bit for the screw to prevent stripping the head.
Accessory Products
In addition to your primary tools, consider these useful accessories:
- Magnetic Bit Holder: Keeps screws attached to the drill bit, especially handy for difficult-to-reach spots.
- Screw Guide: Helps to drive screws straight and to the required depth.
- Torque Adjustment: Most drills come with this feature to prevent over-tightening and damaging the material.
By using these tools and accessories, you’ll tackle your screw-related tasks with greater precision and ease.