
When working on projects that require fastening materials together, it’s important to choose the correct type of screw. Self-tapping, self-drilling and self-piercing screws are the main three common screw options. In this article, we will focus on self-tapping and self-drilling screws. Knowing their differences can help you select the most suitable candidate for the job. While both types create their own holes in the workpiece, they have key distinguishing characteristics in how they function.
This article provides an overview of the two screw types, examines the main difference between self-drilling and self-tapping, and offers guidance on choosing between them for specific projects. By learning the core distinctions between these fasteners, readers will be equipped to select the optimal screws for their assembly or fabrication needs.
What is Self Tapping Screws
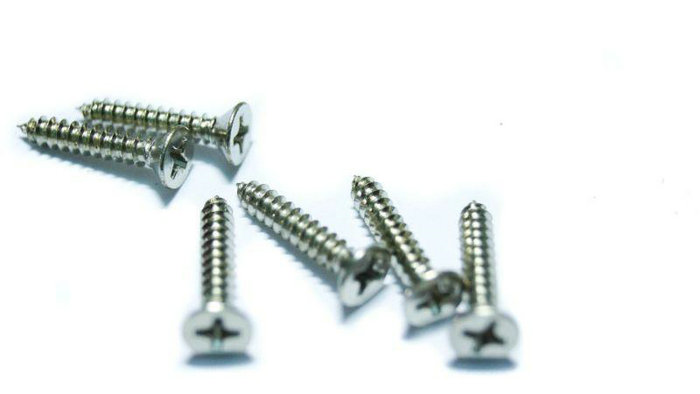
Self-tapping screws are also called metal screws, sheet metal screws, tapping screws, or tapper screws. These screws are typically an essential fastener for countless projects. Their unique ability to tap their own threads makes them invaluable in various materials.
Design Features
These screws feature sharp threads that cut into materials, creating an internal thread to facilitate fastening. The pointed tip of the screw is geometrically crafted to act as a tiny chisel, slicing through metal, wood, or plastic with relative ease.
Self-tapping screws are designed to form their own threads within pre-drilled holes in the material. You don’t have to work too hard; the screws cut their own threads as you drive them in, making them suitable for materials. Important to remember, self-tapping screws need a pilot hole before you start.
Property | Self-Tapping Screws |
Thread Type | Sharp and create own thread first |
Pilot Hole | Required before screwing |
Head Styles | Varied, can be flat, round, or pan |
Materials and Composition
Your choice of tapping screws often boils down to the material they’re made of. Steel is a popular choice, offering durability and strength, while stainless steel resists corrosion robustly. For lightweight needs, aluminum tapping screws are suitable. For more decorative or non-corrosive applications, you might select brass. Each material brings its qualities to the table, allowing for a tailored approach to each particular task.
- Steel: Durable and strong, suitable for most uses.
- Stainless Steel: Excellent for outdoor or corrosive environments.
- Aluminum: Light and less prone to corroding than regular steel.
- Brass: Often used in decorative applications due to its bright, gold-like appearance.
What is Self Drilling Screws
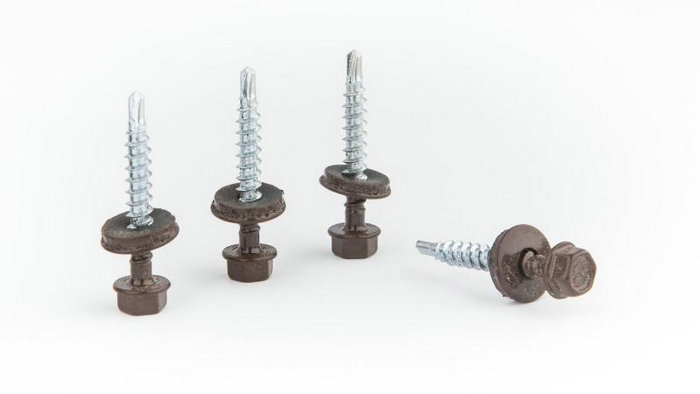
Self-drilling screws are a convenient choice when you’re working with metal such as steel framing or sheet metal. These unique screws are designed to tap their own hole as they are driven into the material, simplifying and speeding up projects.
Drill Point Characteristics
The defining feature of self-drilling screws, also known as Tek screws, is their drill point, which looks like a tiny drill bit. This drill point is specifically engineered to cut through metal. Self-drilling screws do not need for a pre-drilled pilot hole. Here are some specifics:
- Length of drill point: Varies according to the thickness of the material they are designed to penetrate.
- Threads: Usually finer than those of self-tapping screws, allowing for a secure hold in the metal.
Conversely, self-drilling screws act as both a drill bit and a fastener. These are time-savers as they eliminate the need for a pilot hole. They possess a pointed drill-like end, often classified by numbers (1 to 5) indicating their length and thickness.
Property | Self-Drilling Screws |
Drill Point | Number indicates size and thickness |
Pilot Hole | Not required; drills own hole |
Head Styles | Commonly Phillips, hex, or square |
Using Self-Drilling Screws
Your choice of self-drilling screw will depend on the thickness and type of material you are working with. Here’s a simple guide to using these screws:
- Preparation: Ensure your material is stable and mark where you want to place the screw.
- Driving the screw: Use a power drill and match the screw’s drive size to the drill bit.
- Material compatibility: Choose a screw made from a compatible material, like stainless steel, to avoid corrosion.
Self-tapping vs Self-drilling: Performance and Specialized Uses
In choosing between self-drilling and self-tapping screws, your main considerations will likely revolve around the thread-creating process, material penetration abilities, and the time efficiency as well as ease of use provided by each screw type.
Thread-Creating Process
Self-Tapping Screws: They come in two types of self-tapping screws: thread-cutting and thread-forming. Thread-cutting screws remove material to create threads, thus there may be some material displacement. On the other hand, thread-forming screws, also known as thread rolling screws, displace material without cutting it, which can lead to a more secure hold due to material flowing back around the threads.
Self-Drilling Screws: These screws have a pointed tip that acts much like a drill bit. You don’t need to create a pilot hole as these screws are designed to do it for you. Their pointed end efficiently creates the hole and threads in one quick drilling motion, significantly saving time, especially in repetitive tasks or large projects.
Applications in Different Industries
- HVAC: In the heating, ventilation, air conditioning industry, or other general construction tasks, self-drilling screws are frequently utilized to attach components securely, owing to their ability to pierce sheet metals and other substrates without a pilot hole.
- Construction: You’ll find self-drilling screws making work easier when it comes to metal roofing or steel framing, as they efficiently combine drilling and fastening steps.
- Manufacturing: For assembling parts with brackets or aluminum sections, self-tapping screws are often chosen due to their precise threading that can tap into the material without pre-drilling.
Appropriate for Specific Materials
- Sheet Metal: Self-drilling screws are your go-to for working with thin metals, creating the right-sized hole for the fastener while securing materials in a single action.
Material | Screw Type |
Thin Sheet Metal | Self-Drilling |
Thicker Metal | Self-Tapping (pre-drilled) |
- Plastics and Aluminium: Self-tapping screws are ideal for softer materials like plastics or non-ferrous metals such as aluminum. They carve threads into the material, allowing for a secure hold without splitting the workpiece.
Material | Screw Type |
Plastics | Self-Tapping |
Aluminum | Self-Tapping |
Frequently Asked Questions
What’s the difference between self-tapping and self-drilling screws?
Self-tapping screws require a pilot hole to be drilled. They are designed to tap their own threads. In contrast, self-drilling screws have a drilling tip that creates the hole and taps threads in a single operation, which is particularly useful when working with metal.
What types of materials are best suited for self-tapping screws?
Self-tapping screws work well with a variety of materials including wood, plastic, and soft metals. They are ideal for materials that do not require the screw to form its own hole.
When is it ideal to use self-drilling screws instead of self-tapping ones?
Use self-drilling screws when you need to attach materials like metal or hard plastics without the extra step of pre-drilling a hole. They save time in applications involving thicker and harder materials.
Are there any specific situations where self-tapping screws might not be the best choice?
Avoid using self-tapping screws for hard metals or for any material where the force needed to tap the thread could break the screw or damage the material. They may not be suitable for situations where the structural integrity of the material cannot be compromised.
How do self-tapping screws perform in attaching metal to metal applications?
Self-tapping screws can perform effectively in metal-to-metal applications, provided that a suitable pilot hole has been created. However, for thicker metals, self-drilling screws may be more efficient.
What factors should be considered when selecting a self-tapping screw for plastic materials?
Consider the type of plastic, the thickness, and the level of durability required. Choose a self-tapping screw with a sharp point and widely spaced threads to prevent cracking or splitting the plastic material.