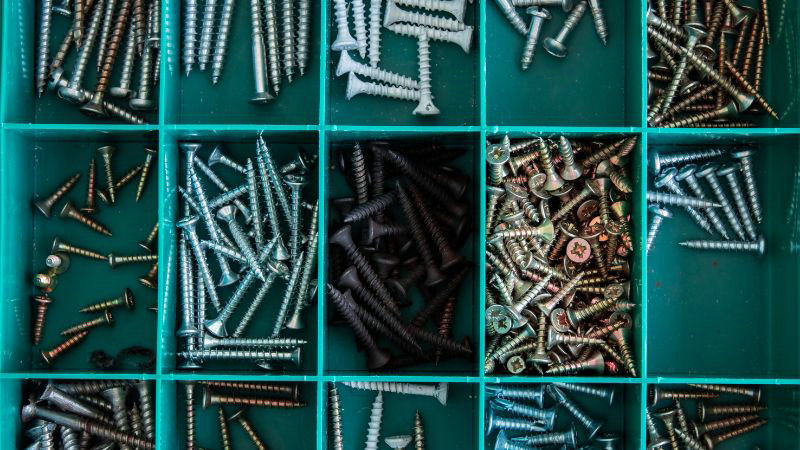
Czym są powłoki elementów złącznych?
Powłoki mocujące są kluczowe dla zwiększenia trwałości i funkcjonalności mocowań. Zapewniają ochronę przed korozją, poprawiają wygląd i mogą być wykonane z różnych materiałów, aby spełnić określone potrzeby.
Powłoki mocujące to warstwy nakładane na części metalowe, takie jak śruby, nakrętki i nakrętki, w celu ochrony ich przed korozją, która występuje, gdy metal zaczyna się zużywać pod wpływem warunków atmosferycznych lub chemikaliów.
Dlaczego elementy złączne wymagają powłok?
Wybór odpowiedniego rozwiązania w zakresie łączników i powłok może mieć duże znaczenie, zwłaszcza w branżach, w których trwałość i precyzja mają kluczowe znaczenie.
W środowiskach takich jak ocean, gdzie problemem może być słona woda i wilgoć, elementy złączne ze stali nierdzewnej mogą pomóc w zapobieganiu rdzewieniu.
W sektorze opieki zdrowotnej elementy złączne są często stosowane w urządzeniach i sprzęcie medycznym. Tutaj powłoki muszą nie tylko chronić przed korozją, ale także spełniać rygorystyczne normy czystości i nietoksyczności.
Oto powody, dla których elementy złączne wymagają powlekania:
- Odporny na korozję:
- Zapobieganie rdzy: Wiele elementów złącznych wykonanych jest ze stali lub innych metali podatnych na rdzę i korozję pod wpływem wilgoci i czynników środowiskowych.
- Zwiększona trwałość:
- Odporność na zużycie i uszkodzenia: Powłoki mogą zwiększyć twardość i odporność na ścieranie elementów złącznych, dzięki czemu będą one trwalsze pod wpływem obciążeń mechanicznych.
- Izolacja elektryczna:
- Zapobieganie zwarciom: W zastosowaniach elektrycznych powlekane elementy złączne mogą pełnić funkcję izolatorów, zapobiegając niepożądanemu przewodzeniu prądu pomiędzy komponentami.
- Specjalistyczna wydajność:
- Odporność na ciepło: W środowiskach o wysokiej temperaturze niektóre powłoki mogą chronić elementy złączne przed degradacją wywołaną ciepłem.
- Odporność chemiczna: W miejscach, w których elementy złączne są narażone na działanie substancji chemicznych lub drażniących substancji, specjalistyczne powłoki gwarantują, że elementy złączne zachowają swoją integralność i wydajność.
Różne rodzaje powłok elementów złącznych
Wybierając elementy złączne, kluczowe jest rozważenie odpowiedniego rodzaju powłoki, która zapewni ochronę i właściwości, których potrzebujesz. Przyjrzyjmy się bliżej różnym dostępnym powłokom.
Powłoki metaliczne
Cynkowanie
Cynkowanie jest szeroko stosowaną, ekonomiczną metodą ochrony elementów złącznych przed korozją. Polega na pokryciu powierzchni metalu cienką warstwą cynku, która działa jak bariera ofiarna przeciwko rdzy.
- Czysty cynk
- Wygląd: Wykończenie w kolorze srebrnym.
- Zalety: Zapewnia odporność na korozję, zachowując jednocześnie metaliczny wygląd łącznika. Nadaje się do zastosowań, w których estetyka ma znaczenie.
- Zastosowania: Części samochodowe, obudowy urządzeń elektronicznych i artykuły dekoracyjne.
- Cynk żółty
- Wygląd: Charakterystyczny złoty odcień.
- Proces: Uzyskano to poprzez proces galwanizacji, który polega na dodaniu pierwiastków stopowych z cynkiem.
- Zalety: Zwiększona odporność na korozję atmosferyczną w porównaniu do czystego cynku. Zapewnia bardziej estetyczne wykończenie w przypadku niektórych zastosowań.
- Zastosowania:Elementy złączne do zastosowań architektonicznych, konstrukcje zewnętrzne i okucia meblowe.
Cynkowanie ogniowe
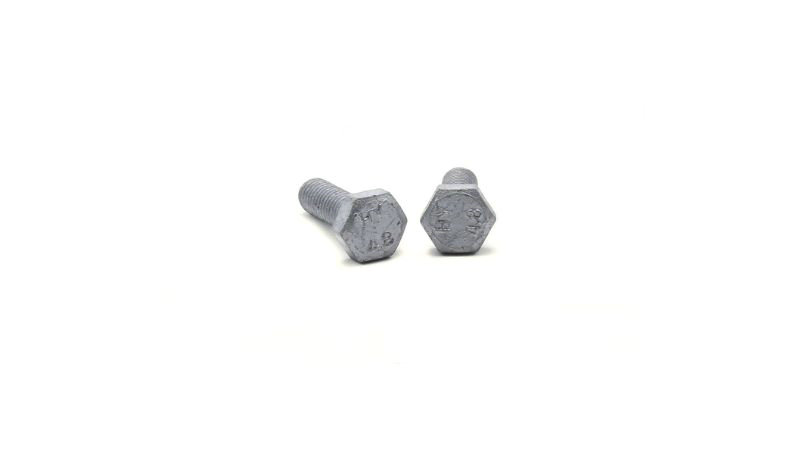
Cynkowanie ogniowe polega na zanurzaniu elementów złącznych w stopionym cynku w wysokiej temperaturze, co skutkuje powstaniem grubej i wytrzymałej powłoki cynkowej.
- Zalety:
- Trwałość: Zapewnia doskonałą ochronę przed korozją, szczególnie w trudnych warunkach zewnętrznych.
- Grubość: Grubość powłoki jest znacznie większa niż w przypadku cynku galwanicznego, co zapewnia dłuższą ochronę.
- Samoleczenie: Jeżeli powłoka ulegnie zarysowaniu, otaczający ją cynk zacznie korodować, chroniąc znajdujący się pod nią metal.
- Zastosowania: Budowa mostów, osprzęt morski, bariery drogowe i rusztowania zewnętrzne.
Kadmowanie
Kadmowanie zapewnia doskonałą odporność na korozję, szczególnie w zastosowaniach wymagających wysokiej niezawodności.
- Zalety:
- Odporność na korozję: Wysoce skuteczny środek zapobiegający korozji, szczególnie w środowisku morskim.
- Smarowność: Zapewnia gładką powierzchnię, która zmniejsza tarcie i zacieranie się elementów złącznych.
- Lutowalność: Ułatwia lutowanie bez uszkadzania powłoki.
- Zagadnienia dotyczące ochrony środowiska: Kadm jest toksyczny i stwarza zagrożenia dla środowiska i zdrowia. Jego stosowanie jest ograniczone w wielu gałęziach przemysłu, co prowadzi do spadku popularności.
- Zastosowania: Elementy złączne dla lotnictwa, sprzęt wojskowy i specjalistyczna elektronika.
Niklowanie
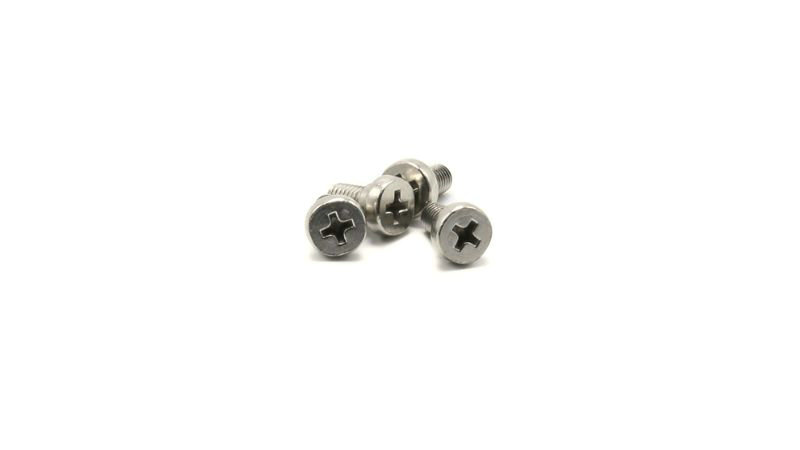
Niklowanie jest cenione za swoje twarde, lśniące wykończenie i doskonałą odporność na korozję. Występuje w różnych formach, każda dostosowana do konkretnych zastosowań.
- Niklowanie Wattsa
- Charakterystyka: Zapewnia jasną, jednolitą powłokę o dobrej ciągliwości.
- Zalety: Zapewnia doskonałą odporność na korozję i nadaje się do elementów wymagających precyzyjnego wykonania.
- Zastosowania: Części samochodowe, podzespoły lotnicze i sprzęt gospodarstwa domowego.
- Sulfaminian niklu
- Charakterystyka: Charakteryzuje się gładszym i bardziej jednolitym wykończeniem niż powłoka Wattsa.
- Zalety: Większa przewodność, zmniejszone naprężenia wewnętrzne i lepsza stabilność wymiarowa. Idealne do późniejszych procesów powlekania.
- Zastosowania: Precyzyjne części maszyn, podzespoły elektryczne i artykuły dekoracyjne.
- Nikiel twardy
- Charakterystyka: Wykazuje zwiększoną twardość i odporność na zużycie.
- Zalety: Zwiększa trwałość i żywotność elementów złącznych poddawanych dużym naprężeniom.
- Zastosowania: Przemysłowe elementy złączne, narzędzia i wysokiej jakości części samochodowe.
- Czarny nikiel
- Charakterystyka: Zapewnia gładkie, ciemne wykończenie dzięki specjalistycznym procesom galwanicznym.
- Zalety: Łączy walory estetyczne z odpornością na korozję. Często używany do celów dekoracyjnych, gdzie pożądana jest powierzchnia nieodbijająca światła.
- Zastosowania: Okucia dekoracyjne, elementy złączne do zastosowań architektonicznych i elektronika użytkowa.
Chromowanie
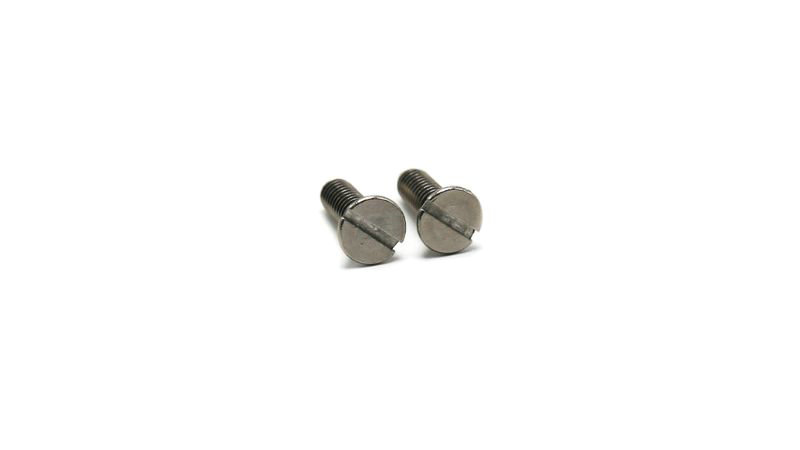
Chromowanie polega na nałożeniu warstwy chromu na powierzchnię elementu złącznego, co powoduje powstanie twardej, błyszczącej powłoki.
- Zalety:
- Twardość: Niezwykle trwałe, odporne na zużycie i ścieranie.
- Odporność na korozję: Zapewnia doskonałą ochronę przed rdzą i matowieniem.
- Estetyczny wygląd: Wysoce odblaskowa powierzchnia poprawia wygląd elementów złącznych.
- Typy:
- Chrom dekoracyjny: Głównie ze względów estetycznych, przy cieńszych powłokach.
- Twardy chrom: Grubsza warstwa zapewniająca większą trwałość i funkcjonalność.
- Zastosowania: Elementy wykończeniowe samochodów, wysokiej jakości elementy złączne maszyn i okucia dekoracyjne.
Anodowanie
Chociaż anodowanie nie jest tradycyjną metodą powlekania, jest to proces elektrochemiczny, który zwiększa grubość naturalnej warstwy tlenku na aluminiowych elementach złącznych.
- Zalety:
- Odporność na korozję: Znacznie zwiększa naturalną odporność aluminium na korozję.
- Odporność na zużycie: Zwiększa twardość powierzchni, redukując zużycie spowodowane tarciem.
- Stabilność koloru: Można barwić na różne kolory, co pozwala na personalizację estetyczną.
- Zastosowania: Elementy złączne dla lotnictwa, obudowy urządzeń elektronicznych i okucia architektoniczne.
Powłoki niemetaliczne
Powłoki fosforanowe
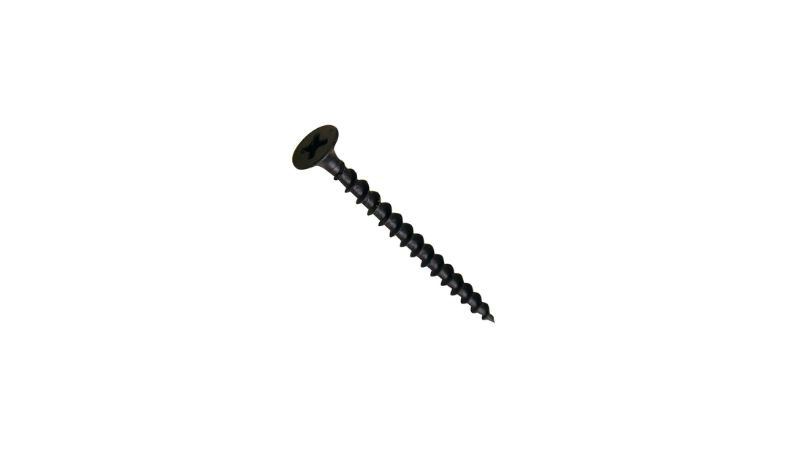
Powłoki fosforanowe nakłada się na powierzchnie metalowe w celu zwiększenia przyczepności farby i zmniejszenia tarcia powierzchni.
- Zalety:
- Odporność na korozję: Tworzy barierę ochronną przed wilgocią i zanieczyszczeniami.
- Przygotowanie do powlekania: Działa jako podkład pod farbę lub powłoki proszkowe, zapewniając lepszą przyczepność i trwałość.
- Smarowność: Zmniejsza tarcie, co minimalizuje zużycie podczas montażu.
- Typy:
- Fosforan cynku: Zapewnia dobrą odporność na korozję i jest powszechnie stosowany jako podkład malarski.
- Fosforan manganu: Zapewnia doskonałą odporność na zużycie i jest stosowany w zastosowaniach wymagających dużej trwałości.
- Zastosowania: Elementy złączne do samochodów, części maszyn i okucia budowlane.
Czarny tlenek
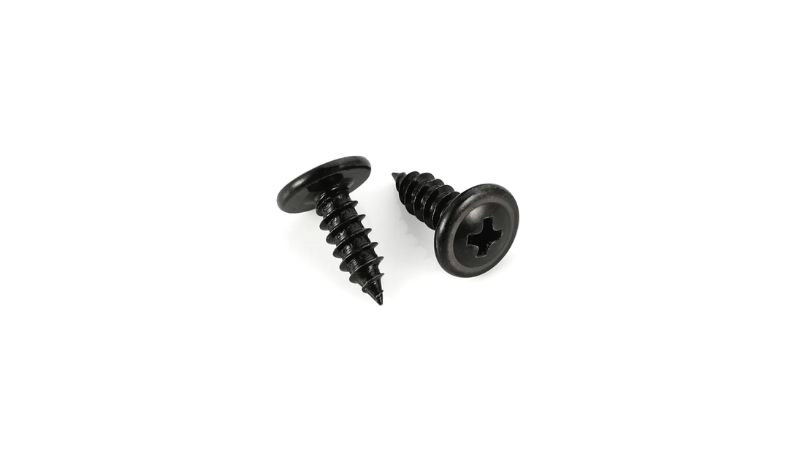
Czarny tlenek to powłoka konwersyjna, która w wyniku reakcji chemicznej nadaje materiałom żelaznym czarną powierzchnię.
- Zalety:
- Estetyczny wygląd: Zapewnia elegancki, matowo-czarny wygląd.
- Minimalna ochrona antykorozyjna: Mimo że stawia pewien opór, jest stosowany przede wszystkim w celach kosmetycznych.
- Zwiększona smarowność: Poprawia powierzchnię mocowania, zmniejszając tarcie.
- Ograniczenia: Zapewnia ograniczoną ochronę antykorozyjną i często jest łączony z dodatkowymi powłokami w celu zwiększenia trwałości.
- Zastosowania: Elementy złączne dekoracyjne, elementy broni palnej i osprzęt elektroniczny.
Powłoka mechaniczna
Galwanizacja mechaniczna polega na wtapianiu proszków metali (takich jak cynk, kadm lub cyna) w powierzchnię elementów złącznych poprzez proces spawania na zimno.
- Zalety:
- Ochrona antykorozyjna: Zapewnia warstwę ochronną bez konieczności stosowania procesów wysokotemperaturowych.
- Jednolite pokrycie: Zapewnia równomierne rozprowadzenie powłoki, także w zagłębieniach.
- Mniejszy stres: Ponieważ jest to proces wykonywany na zimno, minimalizuje on naprężenia cieplne elementów złącznych.
- Zastosowania: Elementy złączne stosowane w elektronice, zespołach samochodowych i maszynach precyzyjnych.
Powłoki organiczne
Powłoka cynkowa płatkowa
Powłoki z płatków cynku łączą w sobie płatki cynku i aluminium, tworząc warstwę ochronną.
- Zalety:
- Odporność na korozję: Zapewnia solidną ochronę przed środowiskami korozyjnymi.
- Stabilność wymiarowa: Utrzymuje wymiary elementu mocującego bez istotnych zmian.
- Łatwość aplikacji: Można nakładać za pomocą tradycyjnych technik malarskich lub natryskowych.
- Zastosowania: Elementy złączne do zastosowań architektonicznych, osprzęt zewnętrzny i elementy infrastruktury.
Powłoki epoksydowe
Powłoki epoksydowe nakłada się jako warstwę ochronną na podłoża metalowe w celu zapobiegania korozji.
- Zalety:
- Trwałość: Wysoka odporność na ścieranie, działanie chemikaliów i degradację pod wpływem środowiska.
- Przyczepność: Tworzy trwałą więź z powierzchnią metalu, zapewniając długotrwałą ochronę.
- Wszechstronność: Dostępny w różnych kolorach i wykończeniach, odpowiednich do różnych zastosowań.
- Zastosowania: Elementy złączne przemysłowe, osprzęt morski i komponenty samochodowe.
Specjalne uwagi dotyczące powłok elementów złącznych
Wybierając powłoki elementów złącznych, należy wziąć pod uwagę, czy spełniają one konkretne wymagania elektryczne i mechaniczne.
Zaspokajanie potrzeb elektrycznych i mechanicznych
W środowiskach, w których przewodnictwo elektryczne jest to problem, twój wybór powłoki może mieć wpływ na wydajność łącznika. Niektóre powłoki są nieprzewodzące i nadają się do zastosowań wrażliwych na elektryczność, podczas gdy inne mogą ułatwiać niezbędne połączenie elektryczne. Kluczowe jest dopasowanie właściwości powłoki do wymagań elektrycznych Twojej aplikacji.
Dla potrzeby mechaniczne, ten współczynnik tarcia odgrywa znaczącą rolę. Właściwa powłoka zapewnia, że Twoje elementy złączne będą miały odpowiedni poziom przyczepności i momentu obrotowego bez powodowania kruchość wodorowa, co jest osłabieniem metalu spowodowanym wystawieniem na działanie wodoru.
Wszystkie wymienione powyżej powłoki są przeznaczone do ochrony elementów złącznych. Jednak konkretne zastosowanie i wymagany poziom odporności na korozję określają najbardziej odpowiednią powłokę. Jeśli nadal nie wiesz, jak wybrać, skonsultuj się z ekspertami z branży Oukailuo. Nasz doświadczony zespół jest gotowy pomóc Ci wybrać odpowiednie materiały do Twojego projektu. Skontaktuj się z nami już dziś!
Często zadawane pytania
Jakie rodzaje powłok są zwykle stosowane w przypadku śrub i wkrętów?
Śruby i wkręty są często pokrywane materiałami takimi jak cynk, ponieważ jest on skuteczny w walce z korozją i stosunkowo niedrogi. Odkryjesz, że ocynkowane elementy złączne sprawdzają się w różnych warunkach ze względu na ich warstwa ochronna, która chroni metal przed wilgocią i innymi czynnikami korozyjnymi.
W jaki sposób powłoka PTFE poprawia parametry elementów złącznych?
Powłoka PTFE zapewnia śliską, nieprzywierającą powierzchnię elementów złącznych. Ta wyjątkowa cecha, którą otrzymujesz w przypadku elementów złącznych powlekanych PTFE, oznacza, że są one mniej podatne na zapiekanie, co jest szczególnie pomocne w zastosowaniach w wysokich temperaturach. Zmniejsza również tarcie, ułatwiając ich dokręcanie i odkręcanie.
Jakie są różnice pomiędzy elementami złącznymi ocynkowanymi a elementami złącznymi chromianowanymi na żółto?
Ocynkowane elementy złączne zapewniają przyzwoity poziom ochrony przed korozją. Jednak dodanie warstwa żółtego chromianu zwiększa ochronę, dając zapięciom dłuższą żywotność. Żółta powłoka chromianowa może również zapewnić bardziej wyraźny złoty kolor, co może być preferencją wizualną w przypadku niektórych zastosowań.
Jak normy dotyczące powłok wpływają na wybór elementów złącznych do zastosowań stalowych?
Normy powłok są krytyczne, ponieważ zapewniają, że Twoje elementy złączne działają zgodnie z oczekiwaniami. Pomagają Ci sprawdzić, czy powłoka wytrzyma określone środowisko, w którym planujesz ich używać, np. w konstrukcjach stalowych, gdzie trwałość i wytrzymałość są najważniejsze.